Probador Instantáneo de Activos Rotativos sin Sensores
- Informe Inmediato Después de la Prueba
- Diagnóstico Automático & Análisis Avanzado
- Cobertura Integral de Fallos
Transforme la Manera en que Monitorea los Equipos Rotativos
El Artesis AMT Pro es un sistema avanzado de monitoreo portátil de condiciones que aprovecha la tecnología patentada de aprendizaje automático y una sólida base de datos de más de 10 millones de perfiles de motores. Proporciona diagnósticos integrales para motores de CA trifásicos, generadores y equipos accionados asociados. Con detección de fallos en tiempo real, informes inmediatos, información sobre eficiencia energética y perspectivas accionables, AMT Pro establece un nuevo estándar para el mantenimiento predictivo.














Características principales
El Artesis AMT Pro es un sistema portátil de prueba de equipos accionados por motor que genera automáticamente un informe de evaluación de condiciones indicando fallos eléctricos, mecánicos y operativos existentes, información sobre el tiempo hasta el fallo, acciones correctivas recomendadas y efectos de los fallos en la eficiencia energética.
Diagnóstico de Fallos Inteligente y Exhaustivo
La característica de diagnóstico inteligente de fallos del AMTPro lo hace muy sencillo de utilizar por el personal de mantenimiento. En lugar de abrumar al usuario final con señales y datos sin procesar, AMTPro proporciona resultados de datos procesados en una forma accionable.
Utilizando una base de datos de más de 10 millones de firmas de fallos, AMTPro detecta y diagnostica problemas hasta con 6 meses de anticipación, garantizando una intervención oportuna.
- Fallos Mecánicos: Cimentación suelta, desequilibrio & desalineación, correa, caja de engranajes, rodamiento, impulsor, aspa de ventilador y más..
- Fallos Eléctricos: Estator, rotor, aislamiento de bobinado, calidad de energía, circuito de potencia y más..
- Problemas de Proceso: Cavitación, obstrucción, sobrecarga, baja eficiencia, filtros obstruidos, turbulencia de flujo y más..
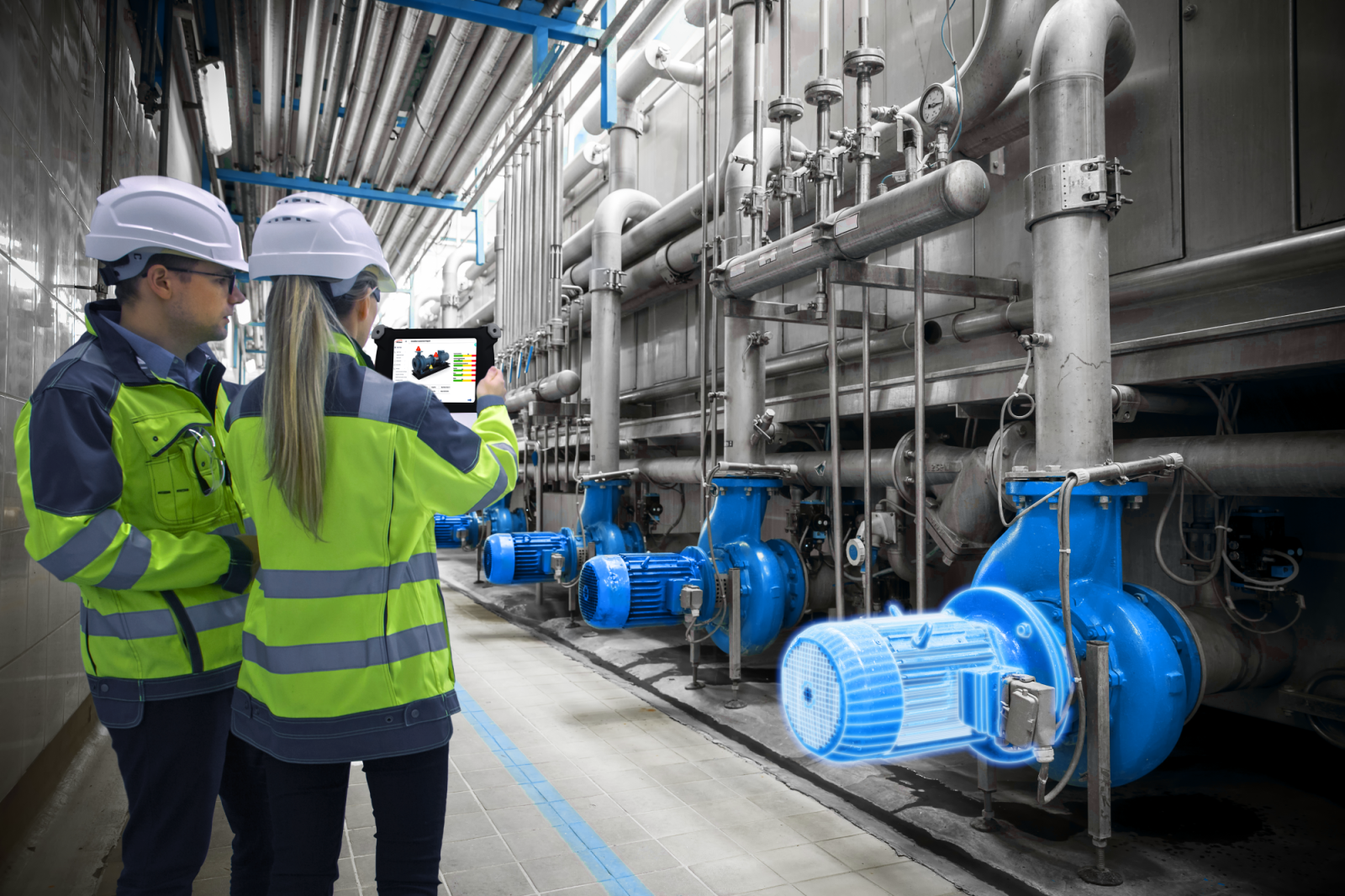
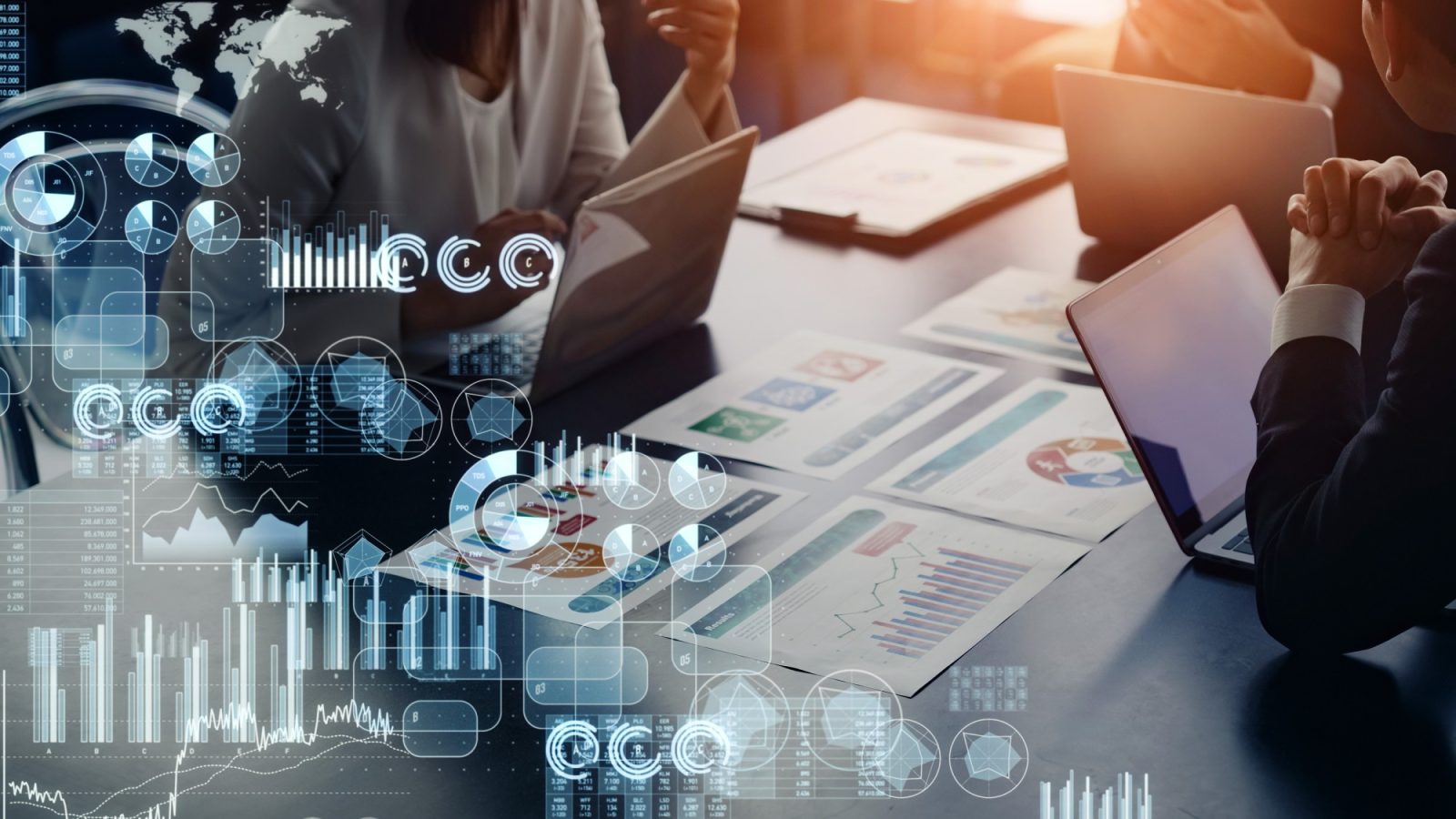
Análisis de Eficiencia Energética y Costos
El consumo de energía es uno de los mayores gastos operativos en cualquier instalación con sistemas extensivos accionados por motores. El módulo de Análisis de Eficiencia y Costos de AMTPro transforma los datos brutos de corriente y voltaje en métricas financieras accionables:
- Detección de Ineficiencias: Identifique ineficiencias causadas por fallos, desgaste mecánico o problemas de proceso.
- Recomendaciones de Dimensionamiento Óptimo del Motor y Eficiencia: Utilizando su extensa base de datos, AMTPro sugiere el tamaño ideal del motor y la clase de eficiencia para su aplicación específica, proporcionando los datos esenciales necesarios para calcular con precisión el ROI.
Diagnóstico Eléctrico y Monitoreo de Potencia
Eleve su comprensión del rendimiento del equipo con el Monitoreo Integral de Potencia de AMT Pro. Esta función avanzada proporciona perspectivas sin igual sobre el consumo de energía y la salud del sistema, asegurando una eficiencia y fiabilidad óptimas.
- Análisis de Voltaje y Corriente: Mediciones precisas de voltaje y corriente trifásicos para detectar desequilibrios e ineficiencias.
- Detección de Armónicos: Evaluación integral de la distorsión armónica total (THD) y sus efectos en la calidad de la energía.
- Monitoreo del Circuito de Potencia: Detecte puntos calientes, problemas relacionados con VFD y desequilibrios capacitivos para garantizar un rendimiento seguro y eficiente del circuito.
- Evaluación de Carga: Determine los porcentajes de carga del motor para optimizar el rendimiento y prevenir sobrecargas.
- Monitoreo del Factor de Potencia: Mejore la eficiencia del sistema identificando y abordando problemas del factor de potencia.
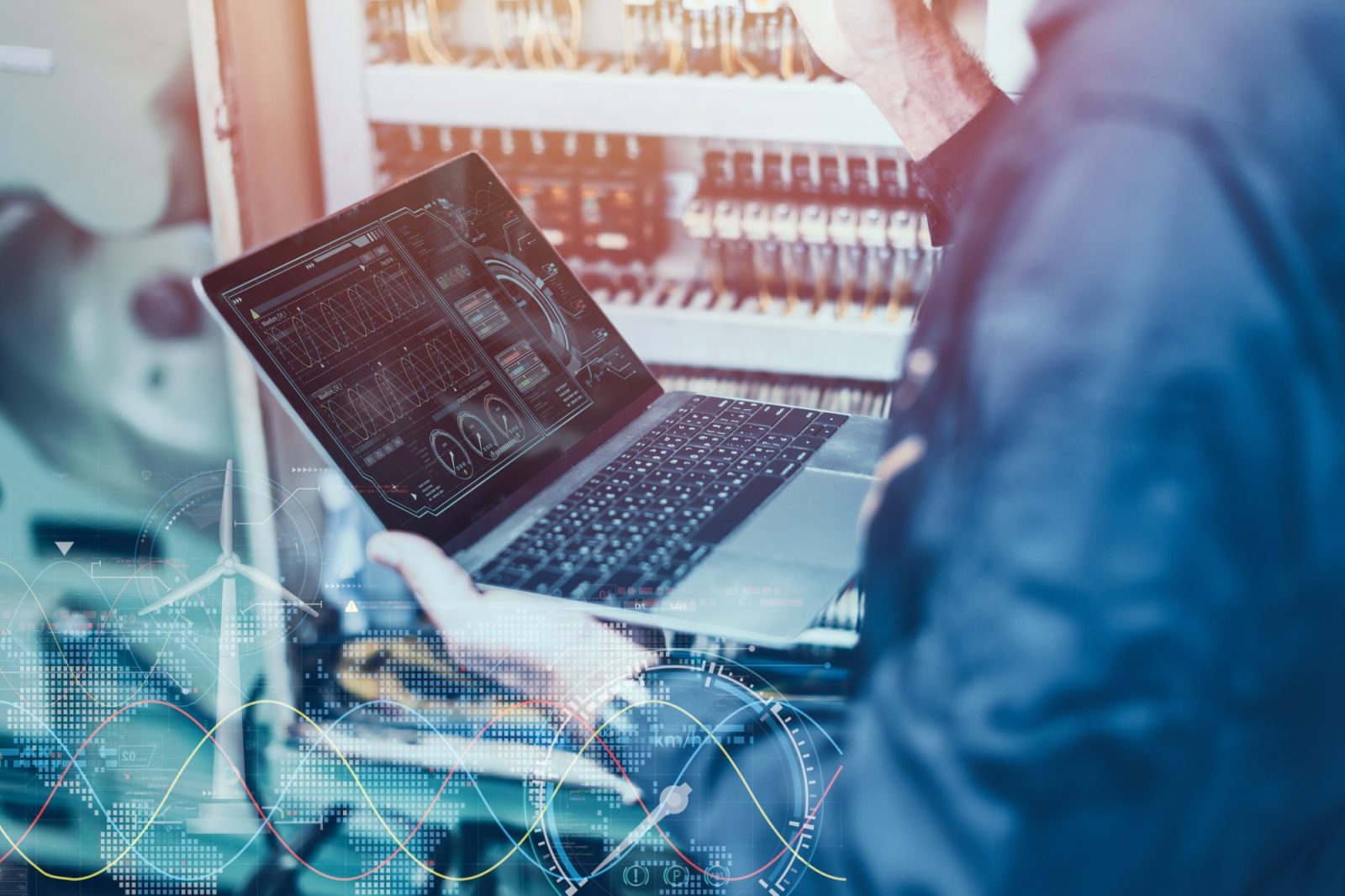
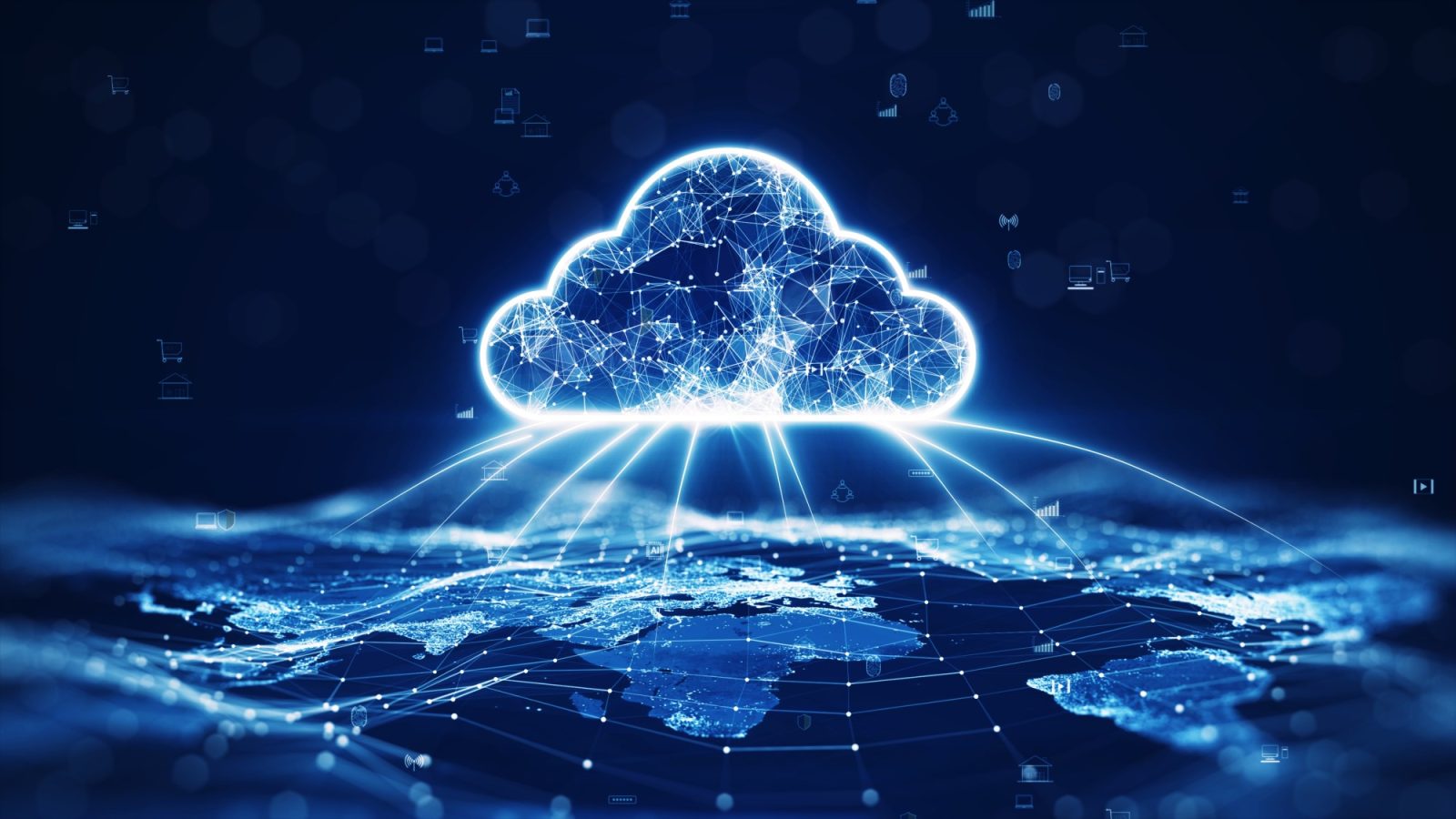
Con la conectividad en la nube de AMT Pro, manténgase conectado a la salud de su equipo y tome decisiones basadas en datos, sin importar dónde se encuentre.
Conectividad en la Nube Sin Problemas
La Conexión en la Nube de AMT Pro asegura que sus resultados de pruebas e informes de diagnóstico se sincronicen instantáneamente con una plataforma segura basada en la nube. Acceda a perspectivas detalladas en cualquier momento, en cualquier lugar, desde cualquier dispositivo.
- Sincronización de Datos en Tiempo Real: Carga inmediata de resultados de pruebas para acceso remoto.
- Almacenamiento Seguro: Mantenga todos los informes de diagnóstico seguros y organizados en la nube.
- Integración IoT: Habilite análisis avanzados y monitoreo remoto a través de plataformas IoT.
- Preparado para la colaboración: Comparta informes sin esfuerzo con su equipo para una toma de decisiones más ágil.
AMT ArPlug: Pruebas de motores en línea simplificadas
El AMT ArPlug mejora el sistema AMT Pro, permitiendo pruebas en línea rápidas y seguras sin necesidad de detener el motor.
Características Clave:
- Configuración rápida: Listo para realizar pruebas en solo 10 segundos.
- Pruebas en línea: Se conecta de manera segura a transformadores y puntos de voltaje mientras el motor está en funcionamiento.
- Seguridad mejorada: La estructura de contacto inteligente previene circuitos abiertos durante las pruebas.
- Optimice sus diagnósticos de motores con pruebas fiables y sin complicaciones.
Video de Artesis AMTPro
Artesis y Jacobs Engineering resuelven con éxito un problema de acoplamiento capacitivo
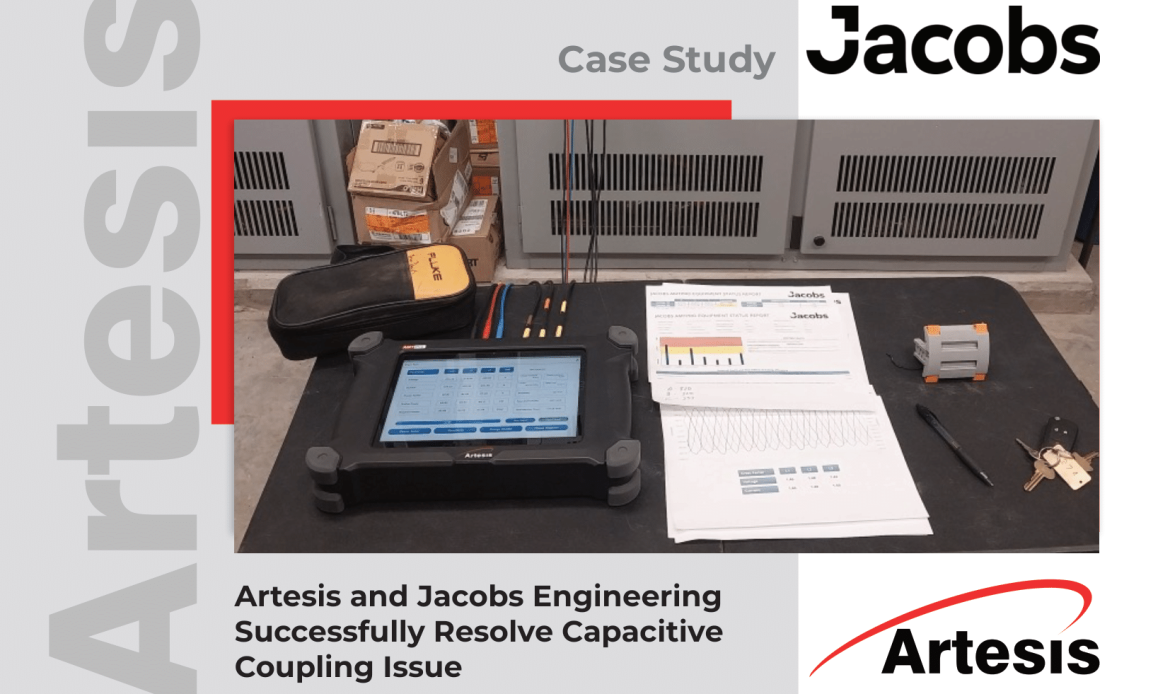