Wind Turbine and Generator Condition Monitoring
- Intelligent Fault Diagnosis
- AI-Driven Digital Twin
- Comprehensive Fault Coverage
Highlights
- Easy installation from a single point with alternator current and voltage information without sensors.
- Maintenance planing information including diagnostic and time to failure
- Easy to use and no need for interpretation by a highly trained person
- Detects and diagnoses exsisting and develoing faults
- Verifies effectiveness of the maintenance action taken
- Unlimited trend recording
- PSD -Power Spectral Density
- Easy installation from a single point with alternator current and voltage information without sensors.
Features
Simple to Install
Installing e-PCM is a simple matter of connecting it to the three supply phases of the generator using simple and inexpensive transducers and mounting it in any convenient panel. It is usually located at the generator control cabinet, requiring very short cable runs and avoiding the need to install equipment in remote or hazardous areas. When first switched on, e-PCM carries out an automatic self-learning process during which the normal operating condition of the equipment is established. Advanced analysis techniques ensure that this training takes account of variables like speed and load, and that existing faults do not result in training errors.
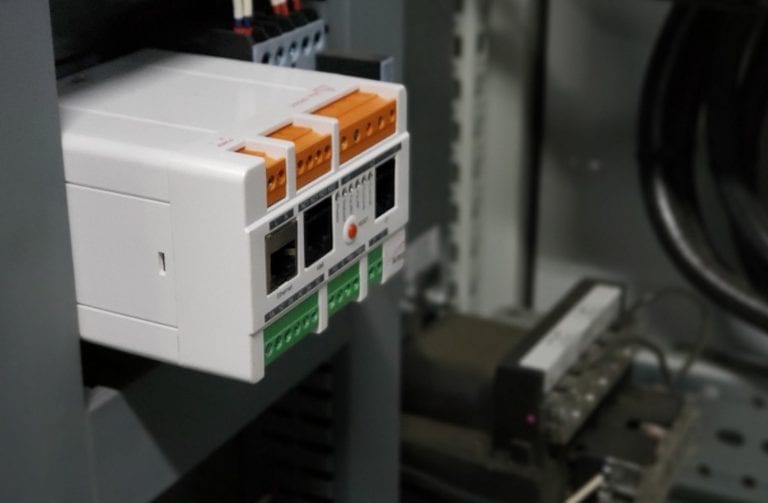
Continuous Monitoring of Your Generator
e-PCM constantly takes measurements and compares them with its reference condition, in order to assess the severity and type of any developing fault. It is able to recognise abnormalities in a wide range of operating states, and is even able to extend its self-learning process when it recognises that it has moved beyond its original learning limits. This allows e-PCM to achieve very sensitive detection of faults without false alarms.
Reliable, Automated Fault Diagnosis
When e-PCM detects a fault, it presents the results of its sophisticated analysis to the user in a simple, compelling traffic light display. This provides local staff with an immediate indication that a problem is developing. Detailed diagnostic information is provided by means of its standard networking facilities, and covers a very wide range of mechanical and electrical problems including imbalance, misalignment, bearing damage, gearbox faults, isolation, and many others. A relay output is also provided so that specific alarm conditions can be annunciated by visual or audible warnings, or communicated to a control system.
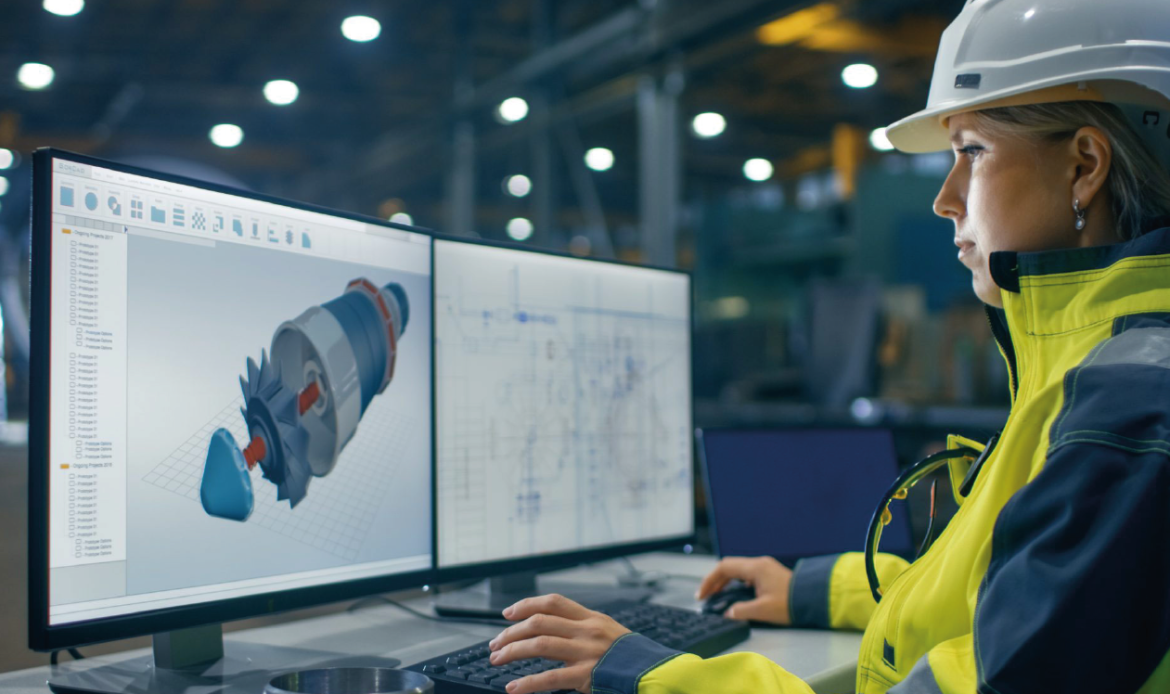
Continuous Monitoring for Wind Turbines












How it works
e-PCM creates a digital twin of generators and their prime movers such as wind turbines. The digital twin is built up during self-learning phase of operation. During this phase the three voltages and three currents are continuously measured and processed using system identification algorithms which determine the model parameters under a full range of operating states.
When a fault starts to develop in either the generator or the prime mover, this has an effect on the current waveform, making the real system behave differently from the model system. This allows e-PCM to use the generator as a sensor that can detect faults in both the generator and the prime mover. e-PCM continuously compares model parameters with those held in the reference model.
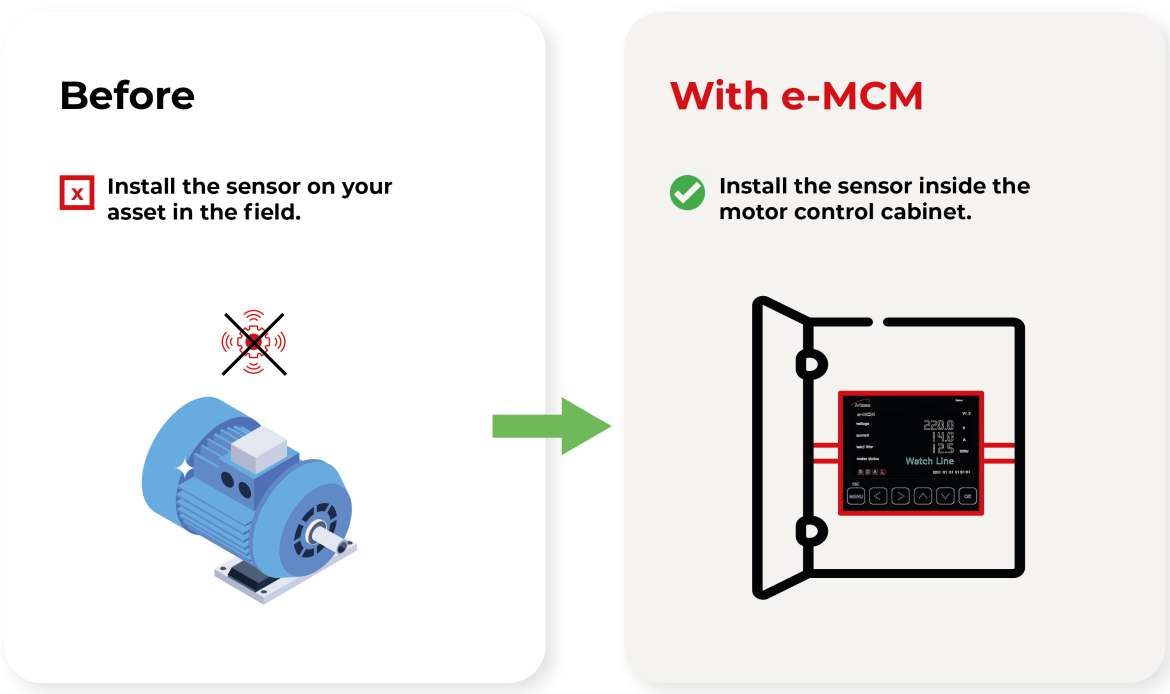
Artesis and Jacobs Engineering Successfully Resolve Capacitive Coupling Issue
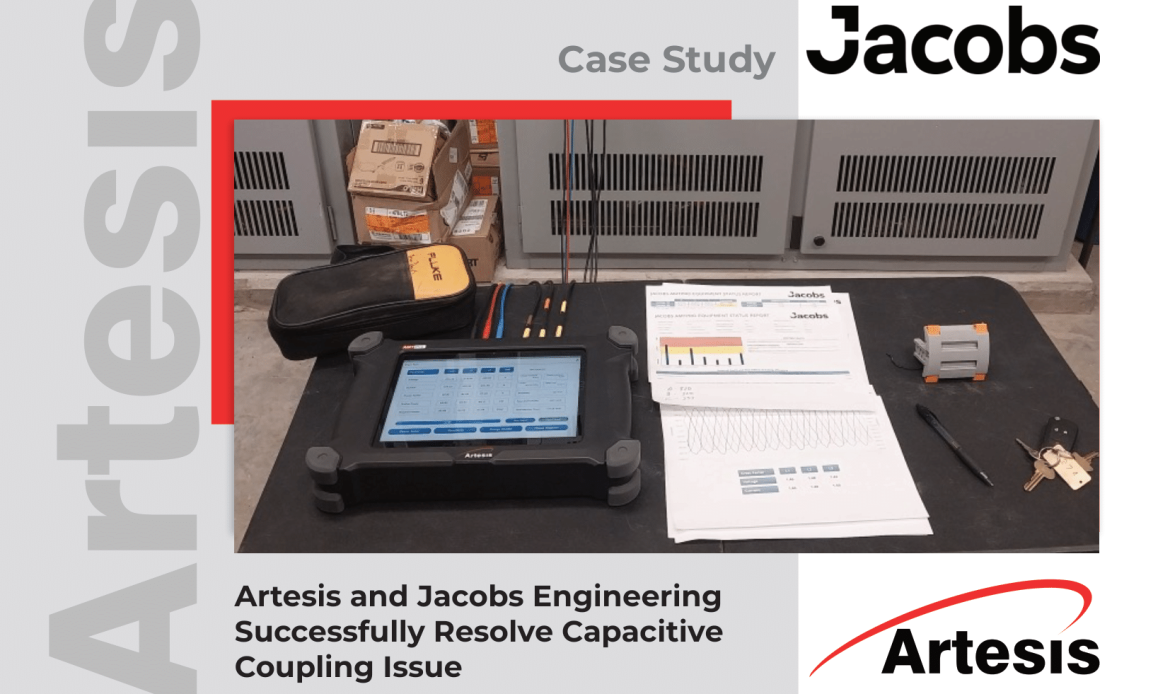
How It Works
e-PCM creates a digital twin of generators and their prime movers such as wind turbines. The digital twin is built up during self-learning phase of operation. During this phase the three voltages and three currents are continuously measured and processed using system identification algorithms which determine the model parameters under a full range of operating states.
When a fault starts to develop in either the generator or the prime mover, this has an effect on the current waveform, making the real system behave differently from the model system. This allows e-PCM to use the generator as a sensor that can detect faults in both the generator and the prime mover. e-PCM continuously compares model parameters with those held in the reference model.
Continuous Monitoring for Wind Turbines
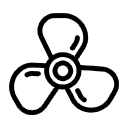
Turbine Blades
- Misalignment
- Mechanical damages
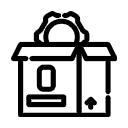
Gear Box
- Wear, crack in gears
- Looseness
- Eccentricity
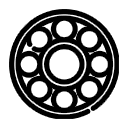
Generator Bearings
- Ring and ball damage
- Crack
- Corrosion
- Lubrication problems
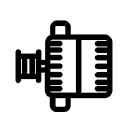
Alternator
- Unbalance
- Axial misalignment
- Cracks in the rotor bars
- Short circuit and insulation problems in wound rotors
- Rotor eccentricity
- Short circuit, insulation weakening and looseness in stator windings
- Heating problems at motor terminal connection points
- Current unbalance and voltage unbalance
- Cable damages and connection faults
Continuous Monitoring for Your Generators
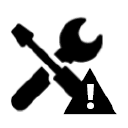
Machine Faults
- Loose Foundation
- Loose Components
- Unbalance
- Misalignment
- Coupling
- Bearing
- Transmission Element
- Rotor faults
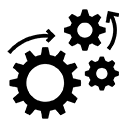
Electrical Faults
- Loose Windings
- Stator
- Short Circuit
- Internal Electrical
- External Electrical
Power Monitoring
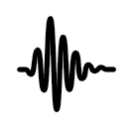
Energy production information
- Instant active power (kW)
- Instantaneous reactive power (kVAr)
- Total active power (kWh)
- Total reactive power (kVArh)
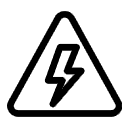
Working hours information
- Total working hours
- Last working hour
- Previous working hour

Energy statistics on equipment
- Active power demand graph
- Day and month summary
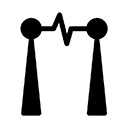
Harmonic Analysis
- THD
- Odd harmonics – 3,5,7,9,11,13