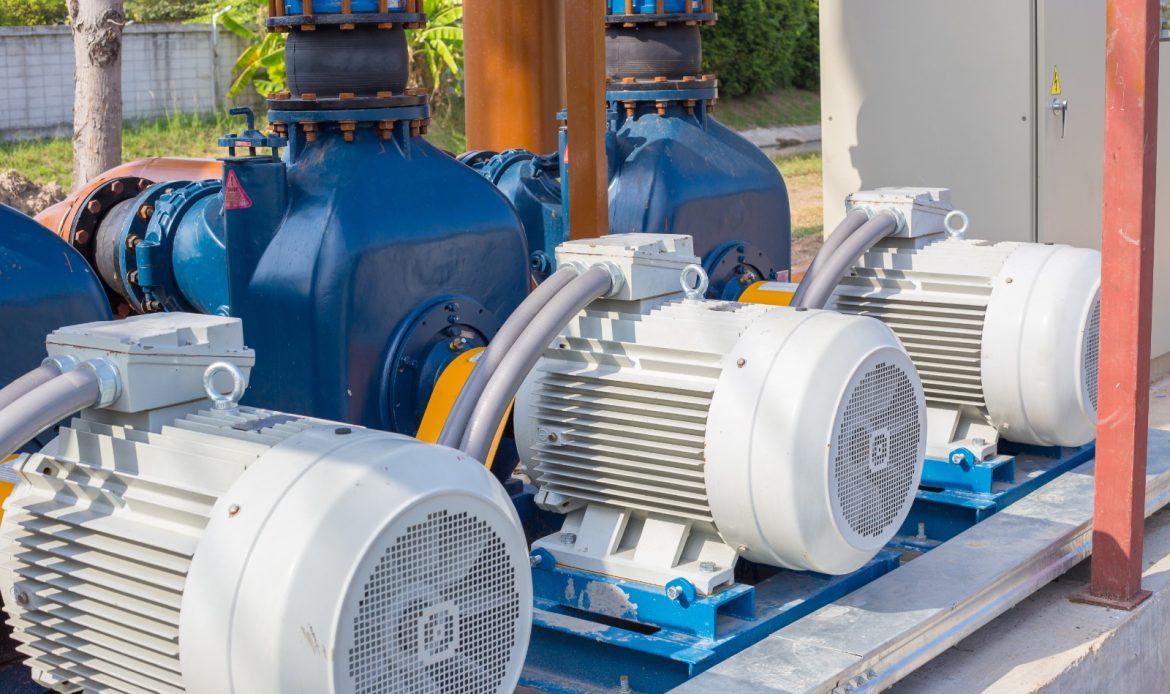
Rotating equipment is an essential part of any process/chemical/fertilizer/oil & gas or power plant and has a versatile role in operations and productivity. Due to massive rotation/use, there is always wear and tear in moving parts which may result in heavy losses in terms of productivity, material, human and reputation in case of failure for in time delivery of the product. It’s a common trend in the industry across the globe to adopt planned maintenance schedules as provided by original equipment manufacturers (OEM). Such planned maintenance makes it possible to curb the sudden faults and saves productivity. With the passage of time, the preventive maintenance concept comes into reality which focuses on eliminating the fault before happening which ultimately makes this possible to increase the equipment life span. Motor, generator, compressors, pumps etc. are key rotating equipment used in the industry. Pumps are an integral part of any plant for the transmission of liquids from one process to another. Pump size and ratings may vary with respect to its application. Due to massive usage, the following types of faults may happen with the passage of time.
Pumps are an integral part of any plant for the transmission of liquids from one process to another
- Sealing failure
- Bearings issues
- Vibration due to impeller unbalance / wear & tear
- Inlet/outlet chocking
- Body leakage
- Shaft Bulging/wearing
- Coupling play / pin damage / fault
- Foundation looseness
- Lubrication fault
- Shaft sleeve wear & tear
- Impeller looseness
Predictive maintenance also called condition based maintenance and there are many predictive maintenance techniques used in industries e.g. current signature analysis. Model-Based Voltage and Current (MBVI) is a new concept that is widely used worldwide and getting popularity due to its cost effectiveness, ease to use/install and high accuracy. This is a condition based monitoring system which is an advanced version of predictive maintenance. MBVI system uses current online data for further diagnoses of the moving parts’ health condition and also capable to store the data. Such data records make it possible for experts to look if there is any deviation in voltage and current waveforms from normal conditions. This system is installed in a Motor/pump or any equipment control panel and measures the input voltage and current. In case of any fault, the waveforms of V & I will change the shape and such a situation will be diagnosed by experts.
Artesis predictive maintenance solution predicts electrical and mechanical failures in pumps up to months in advance.
It’s evident that faults / abnormal conditions do not arise suddenly. Predictive Maintenance has the advantage to early diagnose future faults. Every fault has its own waveform and pinpoints the detection of the faulty area in equipment is also possible. It’s unlike maintenance planning which requires maintenance after the lapse of a specific time but in especially MBVI, the system will tell by itself that maintenance is required at what specific time as per the current situation which not only saves revenue but also production. Saving money makes it happen to be more competitive in the market and is an ultimate edge in the current era of competitiveness. Another benefit of this system is less costly as no such instruments are required to be installed on motors except the voltage-current (VI) module which is highly reliable.
MBVI system is artificially so competitive that from commissioning it collects and stores the data to compare the current readings with previous ones. In this way, accurate analysis is carried out to help the maintenance person at what time and what kind of maintenance is required. Therefore; predictive maintenance is highly desired and becomes an integrated part of any sophisticated rotatory equipment for its safe usage and economical life.