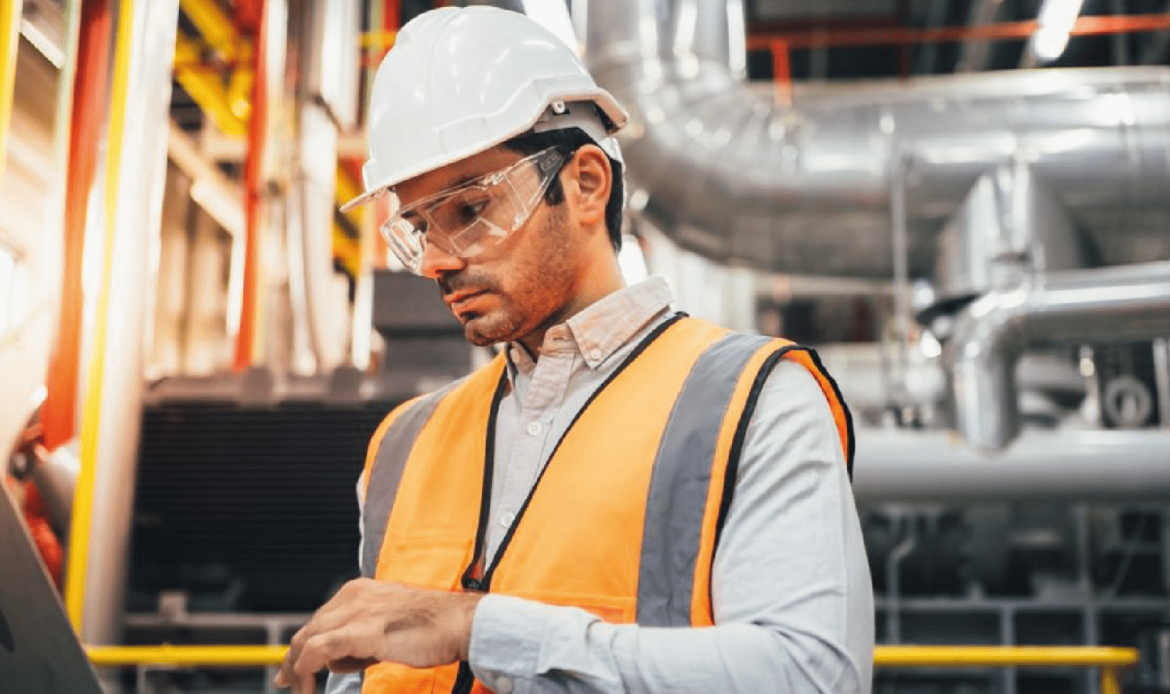
Die komplexe Welt der industriellen Instandhaltung zu navigieren, kann sich anfühlen, als versuche man, ein gigantisches Puzzle zu lösen. Jedes Teil muss perfekt passen, damit die Maschinen reibungslos laufen. Doch wie misst man Erfolg und stellt sicher, dass das Team auf dem richtigen Weg ist? Es geht darum, jene Leistungskennzahlen (KPIs) zu finden, die wirklich von Bedeutung sind. Betrachten Sie KPIs als den Kompass Ihres Teams, der Sie durch die Herausforderungen der Instandhaltungsarbeit leitet und auf Effizienz und Zuverlässigkeit hinweist. Bevor wir uns den Einzelheiten zuwenden, lassen Sie uns den Rahmen dafür setzen, warum die Wahl der richtigen KPIs den entscheidenden Unterschied für Ihr Team ausmachen kann. Wir werden ergründen, wie das industrielle Instandhaltungsteam die Abläufe optimieren und Ihre Ziele effizienter erreichen kann.
Contents
- 1 Reduzierung ungeplanter Ausfallzeiten: Ein Schlüssel zur betrieblichen Exzellenz
- 2 Maximierung der Zuverlässigkeit durch die mittlere Zeit zwischen Ausfällen (MTBF)
- 3 Navigation durch die Gewässer der reaktiven Instandhaltungsarbeitsstunden
- 4 Steigerung der Fertigungseffizienz mit dem geplanten Wartungsprozentsatz (PMP)
- 5 Maximierung der Produktion durch Gesamtanlageneffektivität (OEE)
- 6 Die „richtige“ Lösung zur Unterstützung von Industriellen Wartungsteams?
Reduzierung ungeplanter Ausfallzeiten: Ein Schlüssel zur betrieblichen Exzellenz
Unerwartete Stillstände stellen einen erheblichen Rückschlag für Unternehmen dar, die stark auf kontinuierliche Betriebsabläufe angewiesen sind. Die erschreckende Realität zeigt, dass Industrien durchschnittlich Ausfallkosten von einer Viertelmillion Dollar pro Stunde zu verzeichnen haben, eine Zahl, die die Schwere ungeplanter Stillstände unterstreicht. Alarmierend ist, dass 70% der Unternehmen nicht vollständig darüber im Bilde sind, welche ihrer Anlagen wartungsbedürftig sind, was zu plötzlichen Ausfällen und kostspieligen Perioden der Inaktivität führt. Die Implementierung eines strategischen Wartungsplans könnte die Ausfallzeiten um einen beträchtlichen Anteil reduzieren, in einigen Fällen sogar um mehr als 30%.
KPIs, die sich auf die Erfassung ungeplanter Ausfallzeiten konzentrieren, sind für Instandhaltungsleiter von unschätzbarem Wert und bieten eine Perspektive, durch die die Effektivität von Wartungsstrategien evaluiert werden kann. Das Verständnis der umfassenden Auswirkungen von Ausfallzeiten ist entscheidend, da diese direkt mit Betriebskosten und Produktivitätsverlusten korrelieren, was es für Unternehmen unerlässlich macht, nach minimalen Störungen in ihren Betriebsabläufen zu streben.
Maximierung der Zuverlässigkeit durch die mittlere Zeit zwischen Ausfällen (MTBF)
MTBF, oder Mean Time Between Failures, ist eine entscheidende Kennzahl für jeden im Instandhaltungsbereich. Sie gibt Auskunft darüber, wie lange ein Ausrüstungsgegenstand typischerweise funktioniert, bevor er ausfällt. Betrachten Sie es als eine Bewertung, die Ihnen die Zuverlässigkeit Ihrer Maschinen aufzeigt. Vereinfacht ausgedrückt hilft MTBF Ihnen zu verstehen, wie oft Sie Dinge reparieren müssen, die reparierbar sind, wie Motoren, Pumpen oder Förderbänder. Dies unterscheidet sich von Gegenständen, die nach einem Ausfall nicht repariert werden können, bei denen Sie eine andere Kennzahl, die Mean Time To Failure (MTTF), betrachten würden.
Beispielhaft betrachten Sie ein Fertigungsszenario, in dem eine Abfülllinie in Intervallen betriebliche Ausfälle erlebt. Wenn die Linie über ein Jahr hinweg nur dreimal ausfällt, mit Betriebsperioden von jeweils 120, 150 und 180 Tagen zwischen den Ausfällen, würde die MTBF-Berechnung wertvolle Einblicke in die Zuverlässigkeit der Linie bieten und Wartungsstrategien zur Verbesserung der Betriebszeit und Effizienz leiten.
Diese KPI erfasst die Zeit, die für die Bewältigung ungeplanter Reparaturen oder Notfälle aufgewendet wird und bietet einen Überblick darüber, wie viel Aufwand in die Behebung von Problemen fließt, sobald sie auftreten. Diese Kennzahl ist entscheidend für das Verständnis des Gleichgewichts zwischen präventiven und dringenden Wartungsaufgaben innerhalb einer Organisation. Hohe reaktive Wartungsstunden können auf die Notwendigkeit robusterer präventiver Maßnahmen hinweisen oder häufige Anlagenausfälle signalisieren, was die Gesamtproduktivität und Betriebskosten beeinflusst. Durch die Überwachung dieser Stunden können Teams Trends identifizieren, Ressourcen effektiver zuweisen und einen prädiktiveren Wartungsansatz anstreben.
Steigerung der Fertigungseffizienz mit dem geplanten Wartungsprozentsatz (PMP)
Diese Leistungskennzahl misst den Anteil der Wartungsarbeiten, die im Voraus geplant und terminiert werden, im Vergleich zu reaktiven oder Notfallarbeiten. Diese KPI ist kritisch, da sie direkte Auswirkungen auf die Effizienz und Zuverlässigkeit der Betriebsabläufe hat. Ein hoher PMP deutet auf eine proaktive Wartungsstrategie hin, die zu reduzierten Ausfallzeiten, niedrigeren Reparaturkosten und verbesserter Anlagenlebensdauer führen kann. Durch den Fokus auf geplante Wartung können Teams reibungslosere Abläufe sicherstellen, Störungen minimieren und zukünftige Wartungsbedarfe genauer vorhersagen, was die Gesamtleistung verbessert.
Maximierung der Produktion durch Gesamtanlageneffektivität (OEE)
Diese umfassende Kennzahl bewertet, wie effektiv ein Fertigungsbetrieb seine Ausrüstung nutzt. Sie kombiniert Verfügbarkeits-, Leistungs- und Qualitätskennzahlen, um eine einzige Zahl zu liefern, die den Prozentsatz der Fertigungszeit widerspiegelt, der wirklich produktiv ist.
Ein optimaler OEE-Wert zeigt an, dass eine Anlage Waren mit maximaler Geschwindigkeit, ohne Mängel und mit möglichst wenig Stillstand produziert. Die Verfolgung von OEE hilft Wartungsteams, Verbesserungsbereiche im Produktionsprozess zu identifizieren, um Verschwendung zu eliminieren, Ausfälle von Geräten zu verhindern und die Produktqualität sicherzustellen, wodurch operative Exzellenz und Wettbewerbsfähigkeit gefördert werden.
Die „richtige“ Lösung zur Unterstützung von Industriellen Wartungsteams?
Industrielle Wartungsteams können erhebliche Vorteile erzielen, indem sie Artesis-Technologie in ihre Abläufe integrieren. Diese Technologie vereinfacht den Prozess der vorausschauenden Wartung, ermöglicht eine nahtlose Überwachung und eine einfache, leicht verständliche Datenpräsentation. Mit ihrem intuitiven „Ampel“-Warnsystem und automatisierten Fehlermeldungen, die direkt an Mensch-Maschine-Schnittstellen (HMI) und per E-Mail gesendet werden, sind die Teams in der Lage, potenziellen Problemen voraus zu sein. Die Artesis-Technologie kann potenzielle Ausfälle bis zu sechs Monate im Voraus erkennen und Probleme wie ungewöhnliche Vibrationen, Überhitzung oder Geräuschanomalien hervorheben. Darüber hinaus erleichtert sie die Durchführung präziser Wartungsmaßnahmen mit einer Genauigkeitsrate von über 90%. Dieser proaktive Ansatz verbessert nicht nur die Zuverlässigkeit der Ausrüstung, sondern optimiert auch die Wartungspläne, reduziert Ausfallzeiten und steigert die Betriebseffizienz. Bitte kontaktieren Sie uns, wenn Sie weitere Fragen haben oder eine Demo buchen möchten.