
Businesses waste significant time and money dealing with unscheduled downtime and sudden machine breakdowns. What exactly is a vibration monitoring system and how does it benefit you? A vibration monitoring system serves as a powerful diagnostic tool that measures machinery vibration levels to detect irregularities and potential failures before they turn catastrophic.
The manufacturing world now considers vibration monitoring a crucial part of predictive maintenance strategies. Companies can assess their equipment’s health and performance with remarkable accuracy by measuring and analysing machine vibrations. The applications of vibration monitoring systems range from rotating machinery like motors and turbines to reciprocating equipment such as compressors and pumps. Machine vibration monitoring helps you avoid expensive downtime, reduce repair costs, and make smart decisions about your equipment.
This piece will walk you through everything about vibration monitoring systems. You’ll learn how these systems work, what key characteristics they measure, and discover different types of sensors. We’ll also explore their practical applications in predictive maintenance.
Contents
- 1 How Vibration Monitoring Systems Work in Industrial Settings
- 2 Key Vibration Characteristics Used in Monitoring
- 3 Vibration Measurement Techniques and Sensor Types
- 4 Common Applications of Vibration Monitoring Systems
- 5 From Monitoring to Predictive Maintenance
- 6 Vibration Analysis vs. Electrical Signature Analysis: Why Electrical Signature Analysis is the Smarter Choice for Predictive Maintenance
How Vibration Monitoring Systems Work in Industrial Settings
Vibration monitoring systems are powerful tools that help maintain industrial equipment health. About 90% of machinery gets better with condition monitoring. Vibration analysis stands out as the most popular technique. Let’s get into how these systems work and what they tell us about equipment condition.
Vibration trend analysis for early fault detection
The heart of a vibration monitoring system lies in trend analysis—a process that tracks unusual patterns in machine’s vibration signature. Equipment usually shows signs of internal changes when vibration amplitude shifts by a lot under steady operating conditions.
VA helps diagnose faults early and saves money by cutting maintenance costs and preventing downtime. The system first creates baseline measurements during normal operation. Then it watches for any patterns that don’t match this baseline.
The frequency domain trend monitoring gives crucial details about:
- Fault types within the system
- How bad the fault is
- How long the machine might last
On top of that, these systems can spot vibration signals from specific parts. They identify common issues like bearing problems, loose parts, imbalance, and parts that don’t line up properly.
Amplitude and frequency as indicators of machine health
These systems track two main characteristics of vibration: amplitude and frequency. Each tells us something different about the machine’s health.
Amplitude shows how severe the vibration is and serves as the main sign of machine problems. Under steady operation, big changes in amplitude often mean trouble is brewing. The overall amplitude works well with 4-20 mA output for control systems like PLCs, SCADA, or RTUs.
Frequency helps find exactly where the vibration comes from. Each machine part creates its own unique frequency pattern. This helps technicians quickly find specific problems. Changes in vibration frequency without speed changes might mean trouble.
The core team can spot these issues by understanding these measurements:
- Rotors that aren’t balanced
- Damaged bearings
- Problems with lubrication
- Coupling troubles
- Axles that don’t align
Role of waveform recording in diagnostics
Time waveform recording is crucial for detailed vibration analysis. The waveform captures raw vibration data moment by moment. This reveals vital diagnostic information about the machine’s condition.
Waveform recording brings several benefits:
- Shows peak activity times and overall vibration
- Reveals damping ratios and diagnostic details
- Picks up impacts, modulation, beats, rubs, transients, and random energy bursts
Technicians need to think over sampling frequency and sample numbers when setting up waveform recording. The time waveform should record at least 7-10 shaft rotations during steady operation for the best fault detection.
Frequency analysis finds patterns while time waveform analysis shows the machine’s actual behaviour. A crack in a ball bearing creates distinctive ‘spikes’ in the waveform. This makes it great for finding complex problems that frequency analysis might miss.
Key Vibration Characteristics Used in Monitoring
You need to know the key traits of vibration to use a vibration monitoring system well. These traits help you learn about machine health and spot mechanical problems before they cause major breakdowns.
Amplitude: Severity of vibration
Amplitude shows how intense or severe a vibration is and tells us the most about a machine’s condition. You can measure vibration amplitude in several ways that each give different diagnostic insights:
- Peak-to-peak value – Shows the wave’s maximum movement, which helps assess mechanical clearances and maximum stress
- Peak value – Works best to show short-duration shocks
- RMS (Root Mean Square) value – Gives the most useful measure because it directly links to energy content and how destructive the vibration can be
- Average value – Looks at time history but doesn’t have much practical use
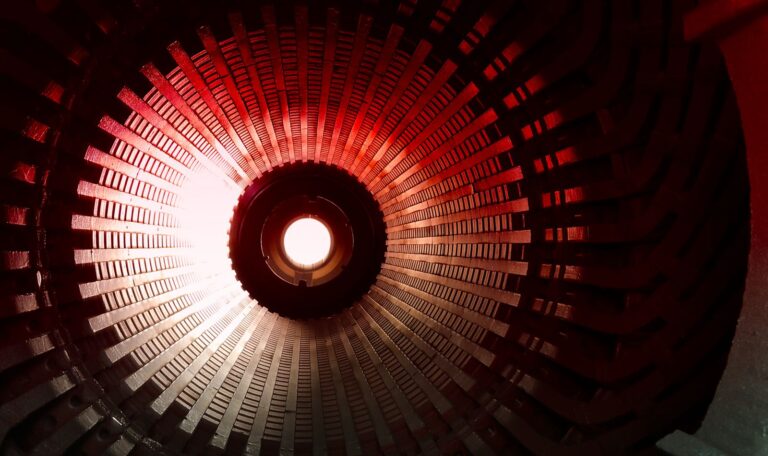
The RMS value plays a key role in vibration monitoring. It takes the wave’s time history into account and shows how much energy the vibration contains. This gives us the best picture of how much damage a vibration might cause.
You can measure amplitude as acceleration, velocity, or displacement based on what you need and the frequency range. Most industries use velocity as their standard to check machine conditions. Displacement works well for low-frequency vibrations, while acceleration helps catch high-frequency vibrations like early bearing problems.
Frequency: Identifying fault sources
Frequency tells us how many times a complete vibration cycle happens in a set time, measured in Hertz (Hz) or cycles per minute (CPM). Frequency is the life-blood of diagnostic measurements because it helps us find exactly which parts create the vibration.
Looking at machine vibrations usually reveals several main frequency patterns that directly link to how different machine parts move. Each machine part creates vibrations at specific frequencies, making its own unique “signature.” A gear with 20 teeth, to name just one example, makes vibrations 20 times faster than the shaft rotation.
By getting into frequency content, technicians can:
- Tell different types of faults apart
- Find which parts have problems
- Figure out what’s wrong mechanically
This makes frequency analysis great for finding gear faults, bearing defects, misalignment, and unbalance without taking the machine apart.
Phase and position: Locating vibration origin
Phase and position measurements round out the vibration analysis toolkit. They give vital spatial details about vibration patterns. Phase shows the timing between two vibration signals at the same frequency, measured from 0° to 359°.
Phase measurements come in two main types:
Absolute phase measures timing between a vibration signal and a fixed point, usually using a tachometer or keyphasor® signal. This measurement helps balance rotors and shows how the machine moves overall.
Relative phase (or cross-channel phase) looks at how two vibration points on a machine relate at a given frequency. This shows how different parts move together and helps diagnose problems like misalignment, loose parts, and bent rotors.
Position information shows the DC component of displacement transducer readings. This helps analyse specific machine problems like misalignment and instability.
Amplitude, frequency, and phase are the foundations of good vibration monitoring. Amplitude shows how bad a problem is, frequency tells us what’s wrong, and phase reveals how parts work together. These three traits give us a detailed picture of machine health.
Vibration Measurement Techniques and Sensor Types
The right sensor choice is vital for any vibration monitoring system. Different sensors perform best at specific frequency ranges and shine in certain applications. These sensors work together to create an all-encompassing monitoring strategy.
Accelerometers for high-frequency detection
Accelerometers stand out as the most accessible vibration sensors because they’re versatile and durable. These devices turn mechanical force into electrical current through the piezoelectric effect. High-frequency accelerometers work best to detect gear mesh problems and bearing faults early. Their measurement range spans from 0.2 Hz to 15 kHz, which helps capture subtle high-frequency signals that point to developing issues.
Today’s high-frequency accelerometers come with sensitivities from 10 mV/g for larger vibrations (up to ±500 g) to 100 mV/g for precise measurements (up to ±50 g). You need to mount these sensors directly on the machine – a standard practise in vibration monitoring.
Velocity sensors for mid-frequency monitoring
Velocity sensors shine in the mid-frequency range (10 Hz to 2000 Hz) where common machine faults happen. These include imbalance, misalignment, and looseness. They’re basically accelerometers with built-in integration circuits that naturally highlight lower frequencies and reduce higher ones.
Velocity measurements relate directly to ISO 10816 standards and provide clear monitoring thresholds. These sensors work great when high-frequency noise like steam leaks or cavitation might overpower regular accelerometer readings.
Proximity probes for fluid film bearings
Proximity probes create an electromagnetic field that interacts with conductive materials using eddy current principles. Unlike seismic sensors that measure absolute casing vibration, these probes track relative movement between the shaft and housing.
Machines with fluid film bearings and rigid bearing housings need these non-contact sensors. They are a great way to get data in refineries, petrochemical plants, and power generation facilities. The probes handle high pressures, chemical exposure, and heat while providing linear measurements that high-speed turbomachinery needs.
MEMS vs piezoelectric sensor technologies
Traditional piezoelectric sensors and modern MEMS (Micro-Electro-Mechanical Systems) technology offer different approaches to vibration sensing. Piezoelectric sensors lead in frequency range and accuracy. They detect vibrations from early-stage bearing failures between 20,000-60,000 Hz.
MEMS accelerometers use capacitive measurement principles and now have better noise levels. They work well in many vibration applications up to 125°C. But MEMS technology usually catches only late-stage bearing failures in low frequencies, missing early warning signs that piezoelectric sensors detect.
Piezoelectric sensors remain the top choice for machine health monitoring that needs early fault detection. MEMS technology fits better in less critical applications where cost and power matter more.
Common Applications of Vibration Monitoring Systems
Vibration monitoring systems serve a wide range of industrial equipment, from rotating machinery to massive structural installations. These systems can detect mechanical issues early by analysing unique vibration signatures that different types of equipment produce.
Rotating machinery: Motors, fans, turbines
Motors, fans, and turbines make up the foundation of most industrial operations and benefit greatly from vibration monitoring. Vibration can wear down components too early, reduce equipment lifespan, generate noise, and create safety hazards. Imbalanced or misaligned rotating assets might crack or break driveshafts and other components. Vibration monitoring helps detect bearing wear 12 to 18 months before bearings need replacement, which lets maintenance teams track wear progression and plan optimal replacement schedules.
Gears and bearings: Detecting wear and misalignment
Nearly all rotating machinery contains bearings and gears as vital components. Many bearings fail too early because of contamination, poor lubrication, misalignment, temperature extremes, poor fitting, shaft unbalance, or misalignment. Bearing failures make up nowhere near 3% of fatigue-related issues. This makes vibration monitoring vital in many planned maintenance schedules since rolling bearings show characteristic vibration patterns as their surfaces degrade. Vibration mechanisms become very complex in gear-rotor-bearing systems due to strong vibration transmission and coupling relationships, which highlights the need for proper monitoring.
Reciprocating compressors and pumps
Reciprocating machinery needs specialised monitoring approaches unlike rotating equipment. Standard vibration measurements that suit rotating machinery don’t work well with reciprocating equipment. Common problems like loose bolts, broken parts, or excessive clearances don’t substantially increase overall vibration until severe damage occurs. Technologies that detect mechanical shock events near the cylinder assembly work better. Frame vibration and crosshead vibration monitoring can warn about developing problems earlier.
Structural monitoring: Bridges and pipelines
Vibration monitoring serves a vital role in civil infrastructure. Structural health monitoring (SHM) systems that use vibration-based techniques have become accessible to more people for bridge safety evaluation. These systems help overcome visual inspection limitations by continuously monitoring structural conditions. Research shows that bridge structure vibration analysis matters because vibrations from dynamic loads – human activities, traffic, and wind – can substantially impact structural integrity.
From Monitoring to Predictive Maintenance
The shift from basic vibration monitoring to complete predictive maintenance shows how maintenance strategies have grown. Vibration monitoring systems are the foundations that help maintenance teams switch from reactive to proactive approaches.
Walk-around vs continuous monitoring methods
Route-based monitoring needs technicians to walk specific routes and collect vibration data on rotating schedules—weekly, monthly, or quarterly. This method captures machine health at specific moments. Continuous monitoring systems use fixed sensors to collect data 24/7.
Each method has its benefits:
- Route-based monitoring: Budget-friendly for multiple assets, needs minimal hardware, and helps allocate resources efficiently
- Continuous monitoring: Gives up-to-the-minute data analysis, spots problems quickly, and cuts repair costs by about 25%
Route-based monitoring suits stable assets that run without issues for a year or more. Continuous monitoring works best for critical assets that could cause bottlenecks, safety equipment, or machines prone to quick breakdowns.
4-20 mA transmitters for control system integration
4-20 mA transmitters combine accelerometers with vibration transmitters in tough industrial housings. These devices create output signals that match overall vibration levels, which makes them perfect for existing control systems.
Their compatibility with process control systems like PLCs, DCS, or SCADA systems is their biggest advantage. These transmitters connect straight into loop-powered systems without losing signals over distance.
Loop-powered industrial vibration sensors measure bearing conditions, lubrication problems, imbalance and misalignment on motors, fans, and pumps effectively. Good system integration lets them protect important plant machines around the clock.
Using vibration data for trend-based maintenance planning
Trend analysis plots vibration levels over time to predict maintenance needs. Maintenance teams can act before failures happen by setting proper alarm thresholds based on industry standards, past data, or manufacturer guidelines.
Teams use three common types of alarm thresholds: absolute, trending, and statistical. This method lets teams schedule maintenance based on actual equipment condition instead of fixed times.
A vibration history database plays a crucial role. Enough trend data helps technicians spot developing issues weeks or months before failure, which turns reactive maintenance into predictive care.
Vibration monitoring systems have become vital tools in modern industrial maintenance strategies. This piece explores how these systems detect early warning signs of equipment failure that can save businesses time and money. We got into the core characteristics these systems measure. Amplitude suggests how severe problems are, frequency points to fault sources, and phase shows how components interact. Together, these measurements give detailed insights into machine health.
Different sensor types meet specific monitoring needs. Accelerometers work best at detecting high-frequency early-stage faults. Velocity sensors focus on mid-frequency problems like imbalance and misalignment. Proximity probes give unique benefits for machines with fluid film bearings. The choice between piezoelectric and MEMS technologies depends on what you just need to detect and how you plan to use them.
Vibration Analysis vs. Electrical Signature Analysis: Why Electrical Signature Analysis is the Smarter Choice for Predictive Maintenance
Aspect | Vibration Analysis | Electrical Signature Analysis (ESA) |
---|---|---|
Principle | Measures mechanical vibrations using accelerometers on the equipment. | Analyzes electrical signals (current & voltage) to detect mechanical and electrical faults. |
Installation | Requires sensors mounted on machinery; may need downtime for setup. | Non-intrusive; can be performed from motor control center or terminals. |
Monitoring Location | Requires physical access to the equipment. | Can be done remotely from electrical panel or switchgear. |
Detection Capabilities | Excellent for detecting mechanical faults (imbalance, misalignment, bearing defects). | Detects both mechanical (e.g. rotor imbalance) and electrical issues (e.g. stator winding faults, voltage imbalance). |
Data Collection | Requires physical proximity and possibly hazardous environments. | Safer and more convenient; data collected from control cabinet without physical access to motor. |
Downtime Required | May require stopping the machine for sensor placement or maintenance. | Typically no downtime; can be conducted on running equipment. |
Environment Sensitivity | Accuracy can be affected by noise, mounting issues, or environmental conditions. | Less affected by harsh environments since no contact with moving parts is needed. |
Skill Requirement | Requires skilled personnel for sensor placement and data interpretation. | Easier to deploy and interpret with modern tools and software. |
Cost Effectiveness | Higher cost over time due to sensor maintenance and access requirements. | More cost-effective in the long term due to minimal setup and maintenance. |
Scalability | Difficult to scale across multiple machines due to physical access needs. | Easily scalable across multiple assets and locations. |
Vibration monitoring works in many industrial settings. It helps detect bearing wear in rotating machinery up to 18 months before replacement becomes necessary. Gear systems just need specialised monitoring because their vibration patterns are complex. Reciprocating equipment calls for unique approaches that focus on mechanical shock events instead of overall vibration levels. These benefits extend beyond machinery to critical infrastructure like bridges and pipelines through structural monitoring.
The shift from simple monitoring to predictive maintenance marks a big step forward in maintenance strategy. Route-based and continuous monitoring methods each shine in different ways, depending on how critical assets are and their failure patterns. Without doubt, integrating 4-20 mA transmitters with existing control systems makes live monitoring of critical equipment possible. Trend analysis changes maintenance from reactive to predictive, so teams can schedule repairs based on equipment’s actual condition rather than fixed times.
Vibration monitoring systems are now must-have tools for modern maintenance teams. Knowing how to spot mechanical issues before they cause catastrophic failures cuts downtime, extends equipment life, and makes the best use of maintenance resources. As technology moves forward, these systems will become more sophisticated, which will boost their predictive capabilities and strengthen their position as the life-blood of effective industrial maintenance strategies.