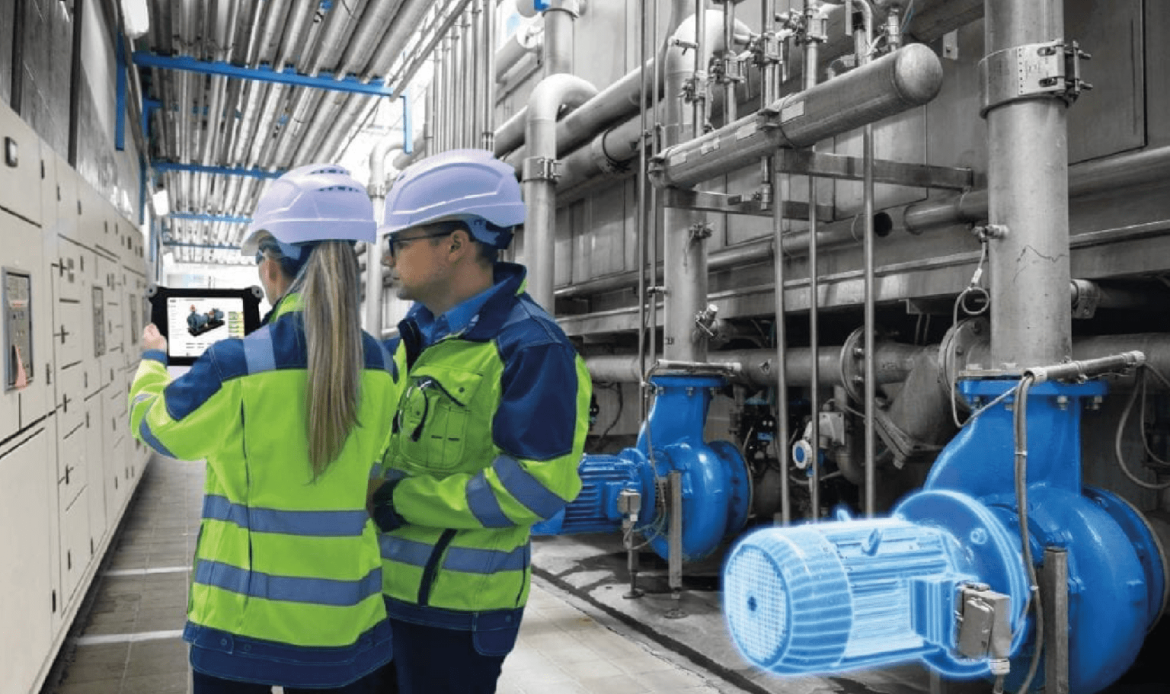
In today’s fast-paced industrial environment, understanding the concepts of maintenance and reliability is crucial for organizations aiming to optimize their operations and ensure the longevity of their equipment. While these terms are often used interchangeably, they represent distinct practices that serve different purposes in asset management. This article explores the fundamental differences between maintenance and reliability, highlighting their significance in predictive maintenance services.
The Importance of Condition Monitoring in the Mining Industry
Contents
Understanding What is Maintenance
Maintenance refers to the activities undertaken to keep equipment and machinery in good working condition. This includes routine inspections, repairs, adjustments, and replacements to prevent breakdowns and prolong asset life. Maintenance can be categorized into several types:
- Preventive Maintenance (PM): Scheduled activities designed to prevent unexpected equipment failures. This proactive approach involves routine checks and servicing based on time intervals or usage metrics.
- Corrective Maintenance (CM): Reactive measures taken after a failure has occurred. This involves identifying the problem, fixing it, and restoring equipment to its operational state.
- Predictive Maintenance (PdM): A data-driven approach that uses condition-monitoring tools and techniques to predict when maintenance should be performed. This minimizes downtime and extends equipment life by addressing issues before they lead to failures.
- Scheduled Maintenance: This type of maintenance involves performing routine tasks at predetermined intervals, regardless of the equipment’s condition.
- Unscheduled Maintenance: Also known as emergency maintenance, this occurs unexpectedly and is often more costly due to downtime and expedited parts and labor.
Understanding What is Reliability?
Reliability, on the other hand, is the probability that an asset will perform its intended function without failure over a specified period under stated conditions. It reflects the inherent performance capabilities of equipment and systems and is often measured using various metrics, including Mean Time Between Failures (MTBF) and Mean Time To Repair (MTTR). Reliability encompasses several key concepts:
- Design Reliability: This focuses on the initial design and engineering of the equipment to ensure it meets performance specifications and can withstand operational stresses.
- Operational Reliability: This is concerned with how well the equipment performs during its operational life, considering factors such as wear and tear, environmental conditions, and usage patterns.
- Service Reliability: This aspect addresses the ability to provide consistent maintenance and support to ensure that equipment operates effectively throughout its lifecycle.
- System Reliability: This evaluates the performance of a system as a whole, taking into account the interactions and dependencies between different components.
The Interrelationship Between Maintenance and Reliability
Please note that while maintenance and reliability are distinct concepts, they are closely related and often influence each other. Reliable equipment typically requires less frequent maintenance, resulting in reduced operational costs and downtime. Conversely, effective maintenance practices can enhance the reliability of equipment by addressing potential issues before they escalate into failures.
In predictive maintenance, the integration of reliability principles into maintenance strategies can lead to significant improvements in operational efficiency. By analyzing equipment data and using advanced analytics, organizations can identify patterns that indicate potential failures, allowing them to schedule maintenance activities proactively.
The Evolution of Maintenance: Condition Monitoring and Predictive Analytics
The Importance of Predictive Maintenance
For instance, consider a manufacturing facility that relies heavily on its production machinery. By implementing a predictive maintenance program, the facility can monitor key performance indicators (KPIs) such as vibration, temperature, and acoustic emissions. Advanced algorithms can analyze this data to predict when a machine is likely to fail, enabling the maintenance team to perform repairs during scheduled downtimes rather than dealing with unexpected breakdowns.
This approach not only reduces maintenance costs but also enhances equipment reliability, resulting in improved productivity and less disruption to operations. Furthermore, with a reliable predictive maintenance strategy in place, companies can optimize their maintenance schedules based on real-time data rather than historical averages.
The Role of IoT in Maintenance and Reliability
Technological advancements have played a pivotal role in enhancing maintenance and reliability practices. The adoption of the Internet of Things (IoT), machine learning, and artificial intelligence has enabled organizations to collect and analyze vast amounts of data from their equipment. This data-driven approach allows for more informed decision-making regarding maintenance activities and reliability assessments.
For example, IoT sensors can continuously monitor the condition of equipment, providing real-time data that can be used to detect anomalies and predict failures. Machine learning algorithms can then analyze this data to identify patterns and trends, leading to more accurate predictions about when maintenance should be performed.
The Bottom Line
In a nutshell, while maintenance and reliability are distinct yet interrelated concepts, both play a vital role in optimizing equipment performance and minimizing downtime. Understanding the differences between these practices is essential for organizations seeking to implement effective predictive maintenance strategies.
By focusing on both maintenance and reliability, companies can enhance their operational efficiency, reduce costs, and improve their bottom line. Embracing a predictive maintenance approach that leverages technology can help organizations achieve these goals.
Artesis offers the leading predictive maintenance services that empower organizations to take control of their maintenance strategies. Our solutions provide effortless monitoring with simple, easy-to-interpret information. With a “traffic light” style warning system and automatic delivery of fault information to Human-Machine Interface (HMI) and email, Artesis ensures that you stay ahead of potential equipment failures, enhancing your operational reliability and efficiency. Choose Artesis for unparalleled predictive maintenance services and elevate your organization’s performance to new heights. Contact us for more details.