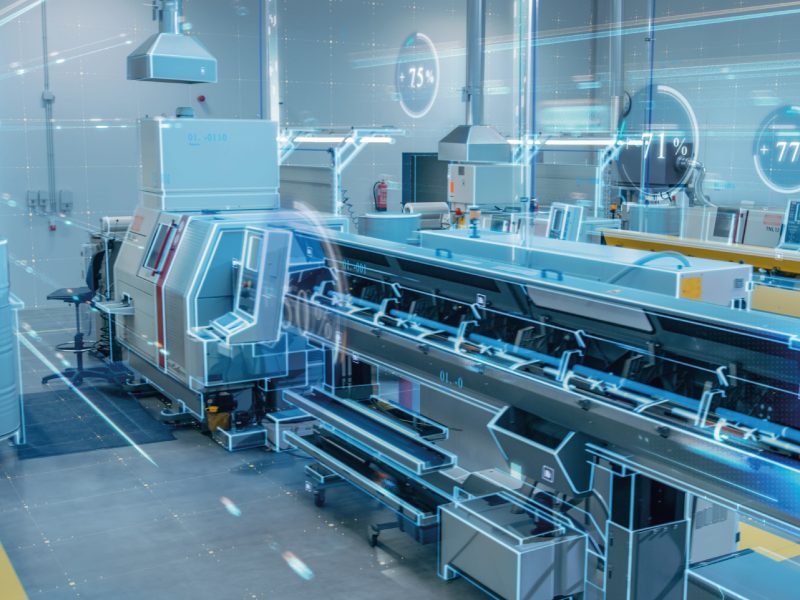
Predictive maintenance is expected to rise rapidly in the following years due to the pressing need to extend the lifespan of aging industrial machinery. Predictive maintenance has come of age in the last five years, and it is now widely accepted. While such systems have seen an evolution over the previous 25 years, they have undergone a revolution in the last five years.
Contents
How Predictive Maintenance Became Mainstream
Predictive maintenance was worth just 1.5 billion globally five years ago. Most systems operated independently and were made up of ‘DIY’ type data-science solutions, limiting the advantages of the technology due to a lack of compatibility and comprehension.
Due to the requirement to extend the life lifetime of failing industrial machinery, the predictive maintenance industry is expected to increase rapidly over the next several years. The requirement to maximize the uptime of assets while simultaneously reducing maintenance costs is due to the increase in demand. In industrial manufacturing plants, there have been more severe rules, regulations, and standards that must be followed in order for predictive maintenance to be effective. As a result, predictive maintenance is an important tool in the workplace.
Furthermore, the rising prevalence of sensors in machinery, automobiles, manufacturing facilities, and other hard equipment areas, among other things, is expected to propel the worldwide predictive maintenance market in the forecast future.
How Do The Next Five Years Look For Predictive Maintenance?
Predictive maintenance will have grown from a solitary, specialized framework or do-it-yourself solution in 2021/2022 to a fast-growing application that is actually delivering high ROI and value to companies.
Analysts anticipate that the industry will continue to develop at a quick pace, reaching a value of $28.2 billion by 2026, aided by Industry 4.0, the Internet of Things, and artificial intelligence. We believe that it will become a component of existing enterprise software, or that firms will select for best-of-breed solutions that seamlessly connect with existing systems in the future. Experts believe that projects that by 2026, 60 percent of IoT-enabled predictive maintenance solutions would be supplied as part of corporate asset management products, an increase from 15 percent in 2021.
Additionally, energy-intensive businesses such as manufacturing will play a key role in addressing climate change and promoting sustainability around the world.
For industrial operations to be sustainable and safer, it is obvious that real-time data, analytics, and predictive maintenance technologies will be required to enable advances in the three major areas of sustainability:
- Reducing the amount of energy consumed by industrial processes
- Lowering the amount of materials and spares wasted
- Increasing the useful life of assets
- Taking steps to reduce health and safety hazards
The Impact of COVID-19 On Predictive Maintenance Market
COVID-19 has had a significant impact on the predictive maintenance market. The hardware industry is expected to be the most affected, according to predictions. The downturn has had an influence on both the good and bad aspects of the predictive maintenance industry. Some manufacturing units have been forced to shut down altogether, which has had a detrimental influence on the predictive maintenance market. As a result of a shortage of manpower and a disrupted supply chain as a result of the covid-19 epidemic, several enterprises are attempting to keep their machinery in good working order.
The Bottom Line: The Future is BRIGHT!
It won’t be wrong to say that predictive maintenance will be as important to industrial organizations in the future as enterprise resource planning (ERP) or financial planning software, because it allows for a level of equipment performance that is commensurate with demonstrating best practice, adhering to industry standards, and generating competitive advantage in the present.