
The condition monitoring industry has been widely using vibration analysis for many years. The use of induction motors in industrial drives is quite common because they are considered dependable, cost-effective, and rugged. In fact, they even became industry workhorses because they play an essential part when it comes to converting electrical energy into mechanical energy. As ensuring safe operation heavily depends on appropriate maintenance, fault diagnostics, safe operation, and operation dependability, there are many traditional techniques and tools used to monitor induction motors. In this article, we take a closer look at motor current signature analysis.
You May be Interested: Motor Condition Monitoring
Even with all the tools used to monitor induction motors for a high degree of dependability, companies were still battling major issues such as reduced motor lifetime and unanticipated system failures. There are several condition monitoring methods such as thermal monitoring and vibration monitoring that need costly sensors, while current monitoring does not need any sort of additional sensors at all. So, let’s first understand motor current signature analysis and see how it is playing a critical role in revolutionizing the condition monitoring industry.
Contents
What is Motor Current Signature Analysis?
It was in the early 1970s when the MCSA concept was originated. Initially, MCSA was proposed as a tool that can be used for monitoring motors in harsh environments and dangerous areas within nuclear power plants. Motor current signature analysis can be described as a technique that helps in determining the induction motor’s operating condition without disturbing production. In other words, it senses an electrical signal that has current components and identifies the faults in the initial stage. Therefore, it plays a pivotal role in preventing damage and diagnosing motor failure. You can follow this link for further reading.
Motor current signature analysis helps in detecting the following:
- Unbalance/ misalignment
- Defective bearings
- Rotor bar damage
- Load issues
- Dynamic eccentricity
- Static eccentricity
Comparison of MCM with Vibration and Current Signature Analysis
How Does Motor Current Signature Analysis Detect Fault Frequencies?
Let’s take an example of the current signal that you acquire from the motor supply without disturbing any operation of the machine. In motor current signature analysis, the frequency spectrum (aka current signature) is acquired by processing the current signal. In case there is a fault, the frequency spectrum becomes dissimilar to the healthy motor. The fault detection of induction motor and condition monitoring is obtained through signal processing techniques because they are cost-effective, and implementing them is pretty easy. Moreover, implementing MCSA helps in getting an accurate analysis of fault.
To identify the exclusive current signature patterns and give a wider dynamic range of different faults, there is the use of decibel (dB) versus frequency spectrum. It helps identify defects such as stator faults, rotor walks, bearing faults and eccentricity, or there could be a combination of these faults.
Motor current signature analysis is effective in predicting both electrical and mechanical errors.
Faults MCSA Can Detect
Here are the faults that motor current signature analysis can detect:
Bearing Faults
There are usually two rings of rolling element bearings. When the operating conditions are normal and there is a balance between good alignment and load, weariness failures typically start with small fissures. It means that they slowly spread to start creating noticeable vibrations and noise levels. Understandably, detecting motor bearings faults is not easy because of different reasons such as misalignments. This is where MCSA steps in to identify defects by detecting frequency components – f 0 (lower frequency) and f 1 (upper frequency).
Broken Rotor Bars
We know that specific induction motors face the problem of broken rotor bars because of laborious duty cycles, but they do not cause the failure of the induction motor. However, they can lead to other damages. For instance, the fault mechanism can break parts and cause mechanical damage and winding failure, directly affecting production and leading to an expensive repair.
Air-Gap Eccentricity
This fault causes an air-gap length that does not remain constant to the stator circumference time and angle. This happens when there is no uniform air gap between the stator and the rotor. There are three types of air-gap eccentricity: Dynamic, static, and mixed eccentricity.
The Role of MCSA in Revolutionizing The Condition Monitoring Industry
Electrical submarine pumps (ESPs) are a perfect example of the importance of MCSA in changing the face of the condition monitoring industry. As ESPs play an essential role in gas and oil operations, they are considered one of the most compliant options because a reservoir does not have enough energy to produce oil and requires an economical lift method to increase fluid flow.
However, the harsh condition in some pumps means that the reliability of the pump is affected. As a result, there are ESP failures due to the presence of fine rock particles, sudden changes in the conditions of the well, presence of gas, and even the rising temperatures. Given that ESP started to fail due to so many external and internal factors, which directly affected production, there was a need for a solution that could mitigate the risks. This is where MCSA stepped in as a perfect solution because it analyzes current and voltage data by using advanced algorithms and helps detect the problems early to prevent any damage.
Faults MCSA Can Detect
Here are the faults that motor current signature analysis can detect:
Bearing Faults
There are usually two rings of rolling element bearings. When the operating conditions are normal and there is a balance between good alignment and load, weariness failures typically start with small fissures. It means that they slowly spread to start creating noticeable vibrations and noise levels. Understandably, detecting motor bearings faults is not easy because of different reasons such as misalignments. This is where MCSA steps in to identify defects by detecting frequency components – f 0 (lower frequency) and f 1 (upper frequency).
Broken Rotor Bars
We know that specific induction motors face the problem of broken rotor bars because of laborious duty cycles, but they do not cause the failure of the induction motor. However, they can lead to other damages. For instance, the fault mechanism can break parts and cause mechanical damage and winding failure, directly affecting production and leading to an expensive repair.
Air-Gap Eccentricity
This fault causes an air-gap length that does not remain constant to the stator circumference time and angle. This happens when there is no uniform air gap between the stator and the rotor. There are three types of air-gap eccentricity: Dynamic, static, and mixed eccentricity.
The Role of MCSA in Revolutionizing The Condition Monitoring Industry
Electrical submarine pumps (ESPs) are a perfect example of the importance of MCSA in changing the face of the condition monitoring industry. As ESPs play an essential role in gas and oil operations, they are considered one of the most compliant options because a reservoir does not have enough energy to produce oil and requires an economical lift method to increase fluid flow.
However, the harsh condition in some pumps means that the reliability of the pump is affected. As a result, there are ESP failures due to the presence of fine rock particles, sudden changes in the conditions of the well, presence of gas, and even the rising temperatures. Given that ESP started to fail due to so many external and internal factors, which directly affected production, there was a need for a solution that could mitigate the risks. This is where MCSA stepped in as a perfect solution because it analyzes current and voltage data by using advanced algorithms and helps detect the problems early to prevent any damage.
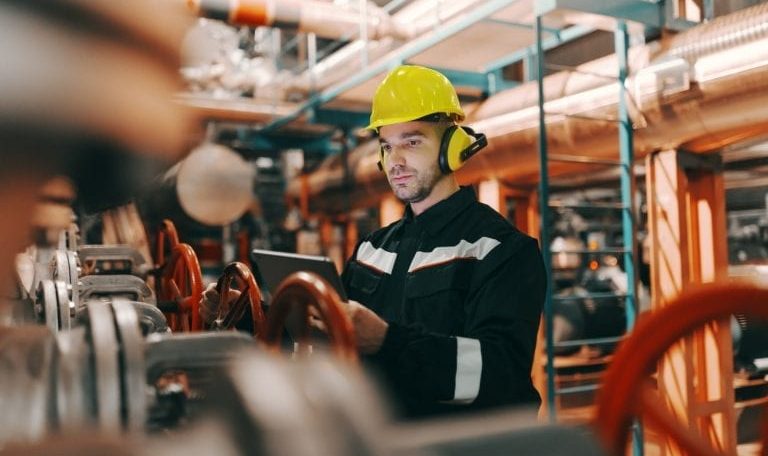
With the introduction of MCSA, previous ESP condition-monitoring tools no longer seem much effective as the MCSA system can be installed in the motor control cabinet (the ideal environment for the system to precisely mitigate the risks). What makes MCSA sensors so effective is that they have the ability to collect data regardless of the operating conditions. Hence, MCSA ensures there are continuous streams of best-quality data.
Now let’s discuss anomaly detection algorithms in the ESP and how each motor and pump had to be inspected. With MSCA, however, there is no need to examine each pump for manual inspections as the engineering team can easily monitor hundreds of pumps. The MSCA-based system has simply eradicated the painstaking, labor-intensive process of manually inspecting each motor and pump. The anomaly detection algorithms also point out which pumps are not working correctly. It helps the maintenance team to focus on those pumps that require urgent fixing. Moreover, it also indicates the root of the problem.
Fault Classification
MCSA has classification algorithms that help identify various patterns associated with different failure mechanisms. For instance, if there is damage to the stator, then the pump cavitation will show a different pattern. If some mechanism fails to work properly, it will leave a mark on the current sine wave, which indicates the maintenance team to check it. Some of the other faults that MCSA can detect are:
- Overheating and sparking due to broken or damaged rotor bars
- There is air-gap eccentricity
- There is bearing damage
- Load effects
- Cavitation
- Wear and tear effects on the equipment
The Bottom Line
There is no denying that the MCSA-based condition monitoring tool is a big addition to ESPs. It has tremendously assisted in lowering maintenance costs, reducing downtime (which was often unplanned), and minimizing environmental and safety risks. It will not be wrong to say that the latest MCSA tools are even more effective because the sensor systems are installed in the MCCs instead of installing them on the asset. Overall, motor current signature analysis is the best technology as it delivers highly selective yet cost-effective online monitoring for different industrial machinery.