
Elevating Pharmaceutical Operations: Artesis Predictive Maintenance for Enhanced Efficiency, Quality, and Growth






Elevating Pharmaceutical Operations: Artesis Predictive Maintenance for Enhanced Efficiency, Quality, and Growth





Key Benefits


· Supports proactive maintenance strategies to ensure uninterrupted production and regulatory compliance.


· Identifies performance deviations that could lead to energy inefficiencies or production downtime, enabling timely corrective actions.


· Reduces maintenance expenses by identifying issues early, preventing costly production halts or compliance failures.


· Can be seamlessly integrated into existing manufacturing systems without significant changes to infrastructure.


· Extends the lifespan of machinery, ensuring consistent production and reducing total cost of ownership.


· Facilitates remote monitoring to ensure compliance with Good Manufacturing Practices (GMP) and enhance operational oversight.


· Suitable for critical applications such as pumps, mixers, conveyors, and air handling systems essential in the production environment.


· Perfect for cleanrooms and controlled environments where minimal physical interference is critical.
Incorporating predictive maintenance from Artesis into pharmaceutical operations enables companies to navigate the industry’s demanding timelines, reduce costs, enhance reliability, and promote sustainable growth while ensuring higher quality standards.
Environment Control
“Real-Life Scenario: Air Handling Unit Malfunction and Consequences”
Imagine a pharmaceutical facility relying on precise environmental control for production. In this setting, an air handling unit malfunction occurs, disrupting the carefully regulated temperature and humidity. If undetected, this glitch could lead to a chain of consequences.
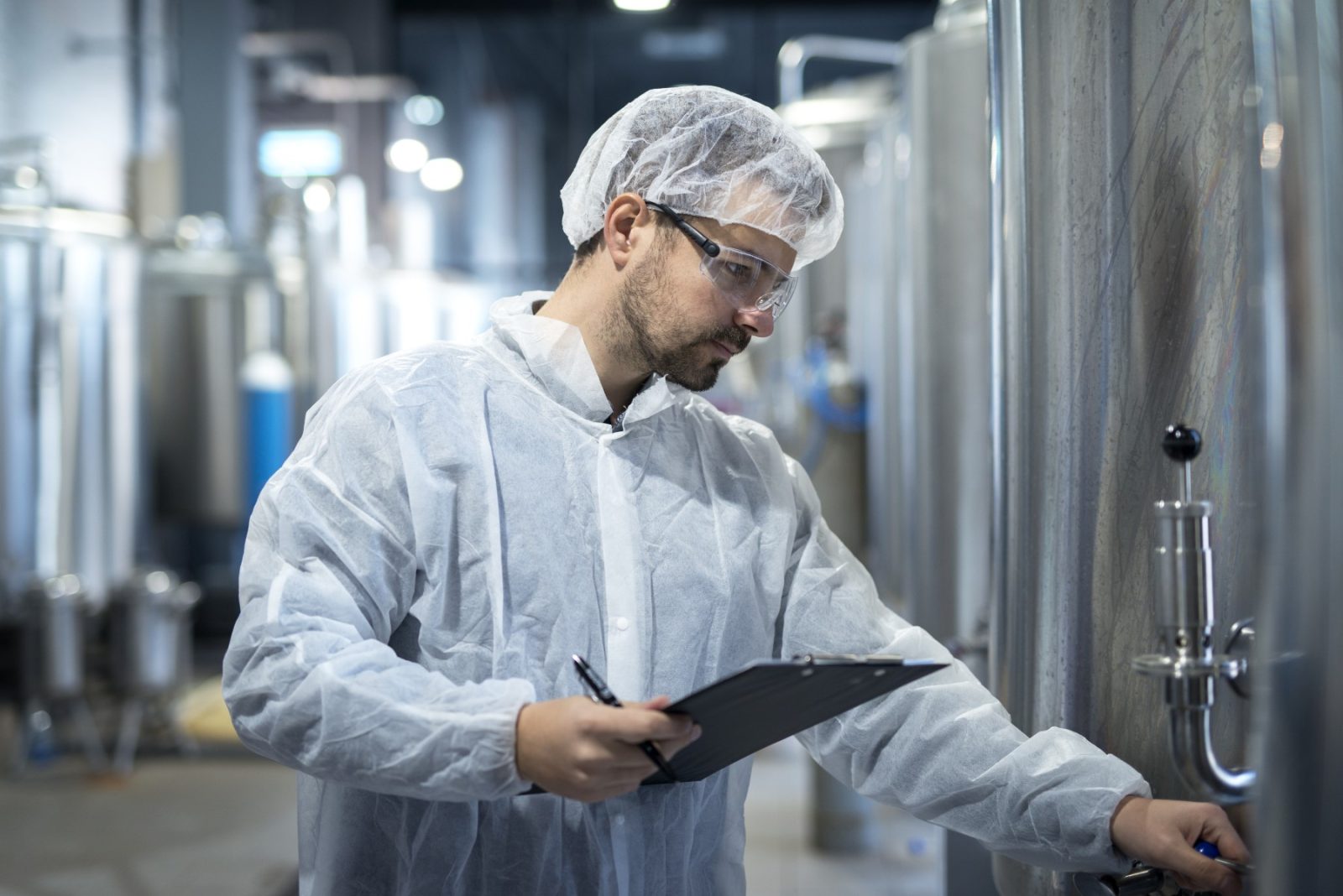
Consequences
Product Quality Compromise
Operational Disruption
Safety Hazards
Regulatory Compliance Concerns
Manufacturing Process
In the intricate web of production, the significance of small pumps, motor-driven mixers, and agitators in batch reactors often goes unnoticed. Yet, a failure in these seemingly minor components can lead to a substantial batch loss. Artesis simplifies the monitoring of these machines, eliminating the need for additional wiring or direct contact with the production line.
Moreover, Artesis ensures a seamless manufacturing process by monitoring conveying systems, guaranteeing a smooth transition from one station to another. In the broader manufacturing spectrum, service equipment like water for injection and deionized water systems is vital. Artesis monitors feeding and supply pumps within these systems, detecting both mechanical and electrical issues such as misalignment, loose foundation, bearing faults, and load fluctuations.
Importantly, Artesis operates within control panels, posing no threat to regulatory compliance in the production process. This means you can enjoy the benefits of advanced monitoring without any concerns about regulatory interference.
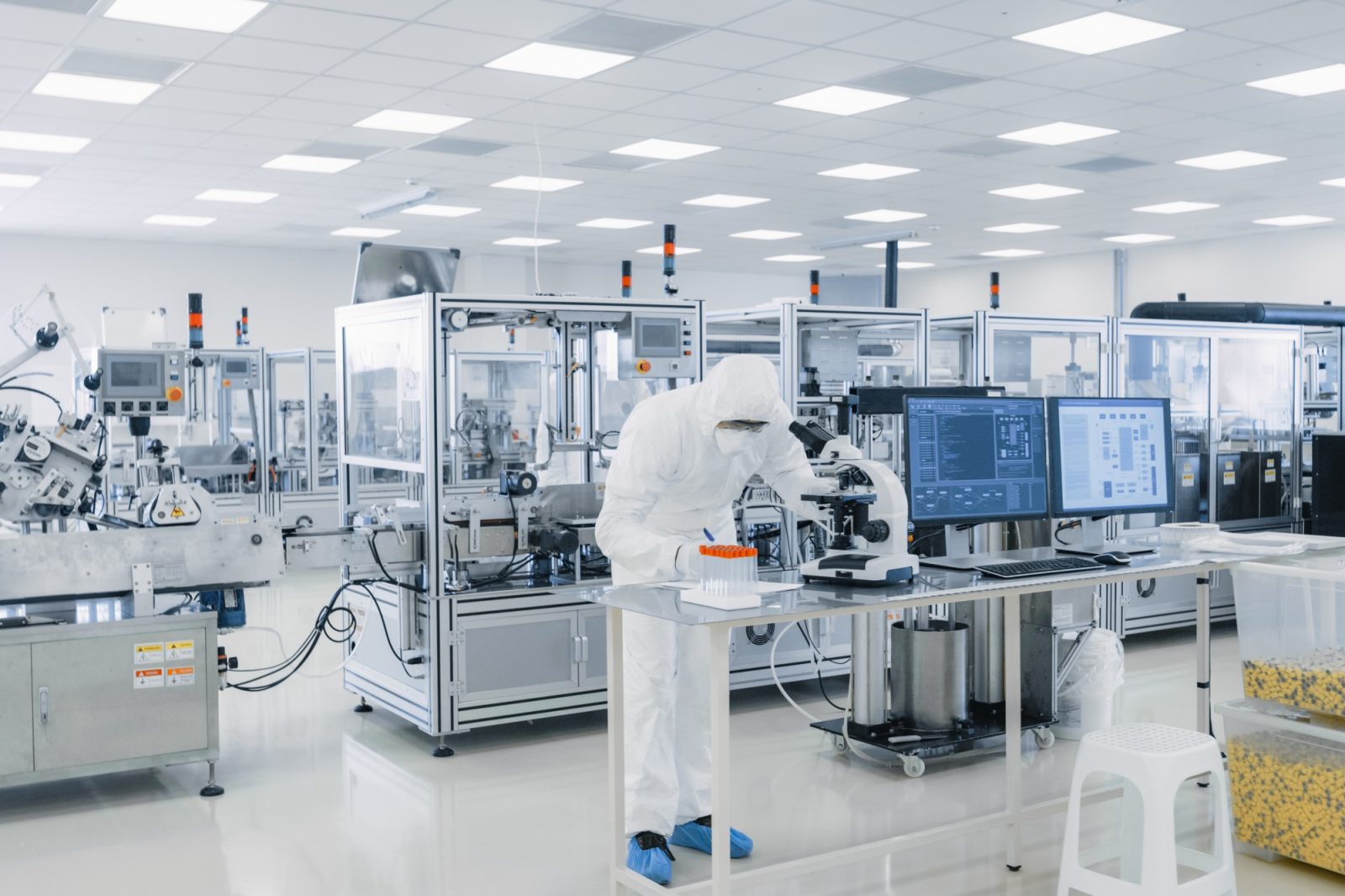
Artesis Intervention: Artesis’s monitoring technology swiftly detects the air handling unit malfunction. This timely intervention prevents product quality compromise, ensures operational continuity, maintains a safe working environment, and upholds regulatory compliance. Artesis acts as a safeguard, ensuring pharmaceutical production stays on track with precision and reliability.
Application Areas in the Pharmaceutical Sector


Granulators: Ensuring fault-free operation of granulation equipment used in drug manufacturing.
Tablet Presses: Monitoring electric motors and systems for consistent operation in tablet compression processes.


Centrifugal Pumps: Ensuring optimal performance of pumps used for transferring liquids and maintaining consistent flow rates.
Dosing Pumps: Monitoring precision pumps for accurate delivery of active ingredients in manufacturing.


Chillers and Cooling Systems: Ensuring reliable operation of equipment used to maintain precise temperature control.


Effluent Treatment Plants: Ensuring the reliability of motors and pumps in wastewater treatment to meet environmental regulations.


Refrigeration Compressors: Ensuring fault-free operation of compressors in cold storage and cryogenic systems.


Labeling and Sealing Machines: Ensuring reliability of motors and drives to maintain packaging efficiency.


Dryers: Ensuring efficient operation of motors and fans in spray and vacuum drying systems.


Generators: Ensuring fault-free operation of backup generators for uninterrupted power supply.


Artesis and Jacobs Engineering Successfully Resolve Capacitive Coupling Issue
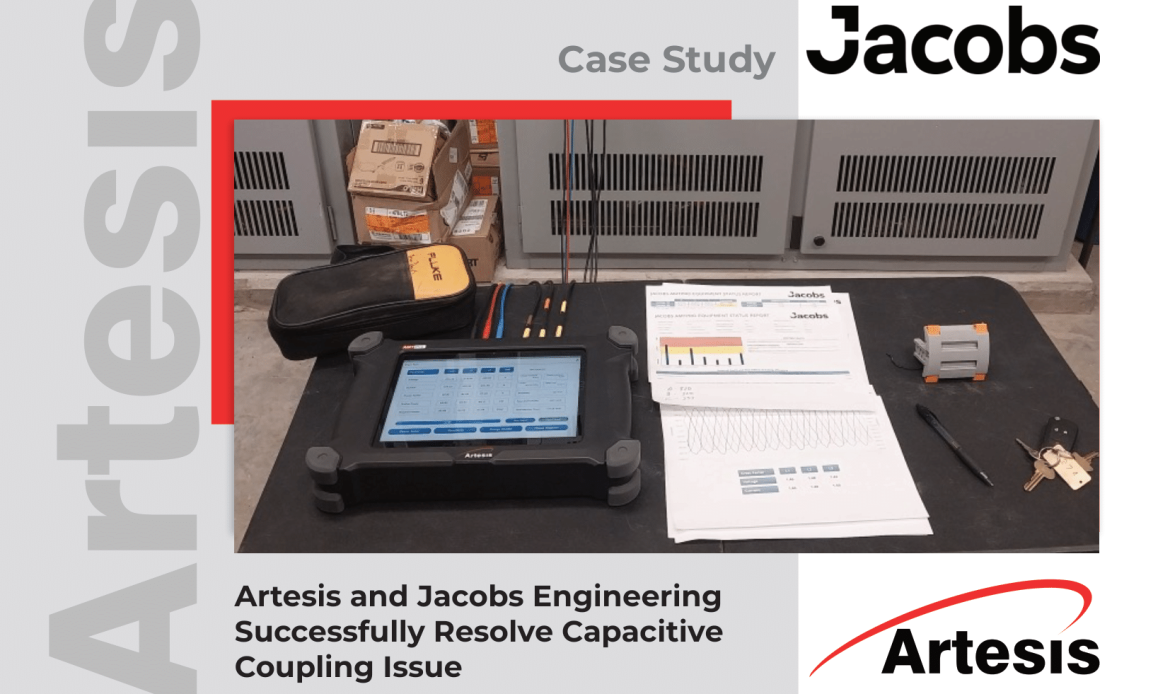