
Condition monitoring and asset management of Oil & Gas assets are hypercritical and difficult.






Condition monitoring and asset management of Oil & Gas assets are hypercritical and difficult.





Key Benefits














Well Drilling and Pumping
Around 60% of the electric motors used in the oil and gas industry are used to drive pumping systems, being well pumping an essential upstream activity in the industry. Monitor all motors connected to the different pumps in your wells to control the mechanical and electrical conditions at any time and without the need to reach hazardous and remote areas. In addition, you will be able to monitor the mud pumps of your drilling rigs to make sure the drilling process is properly completed.
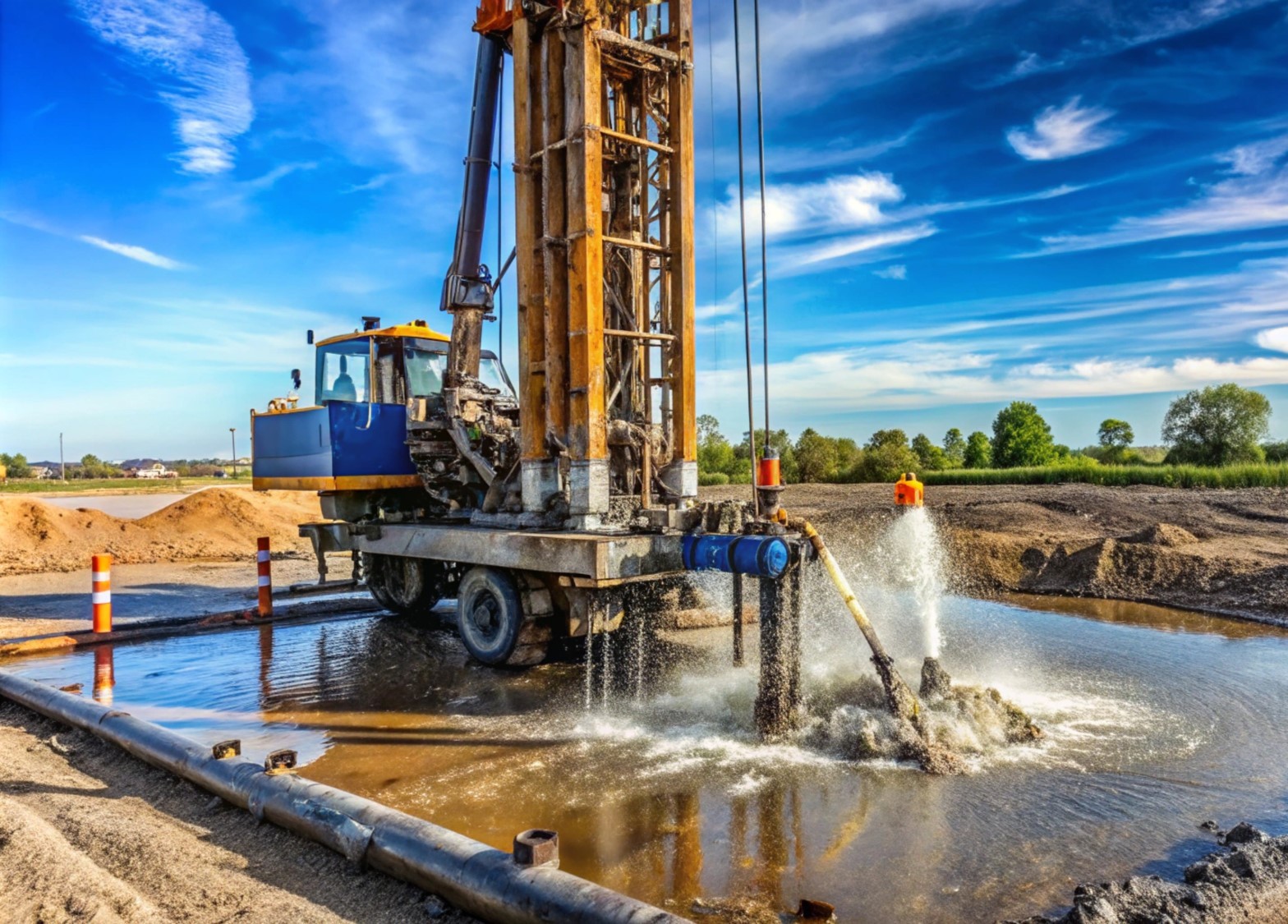
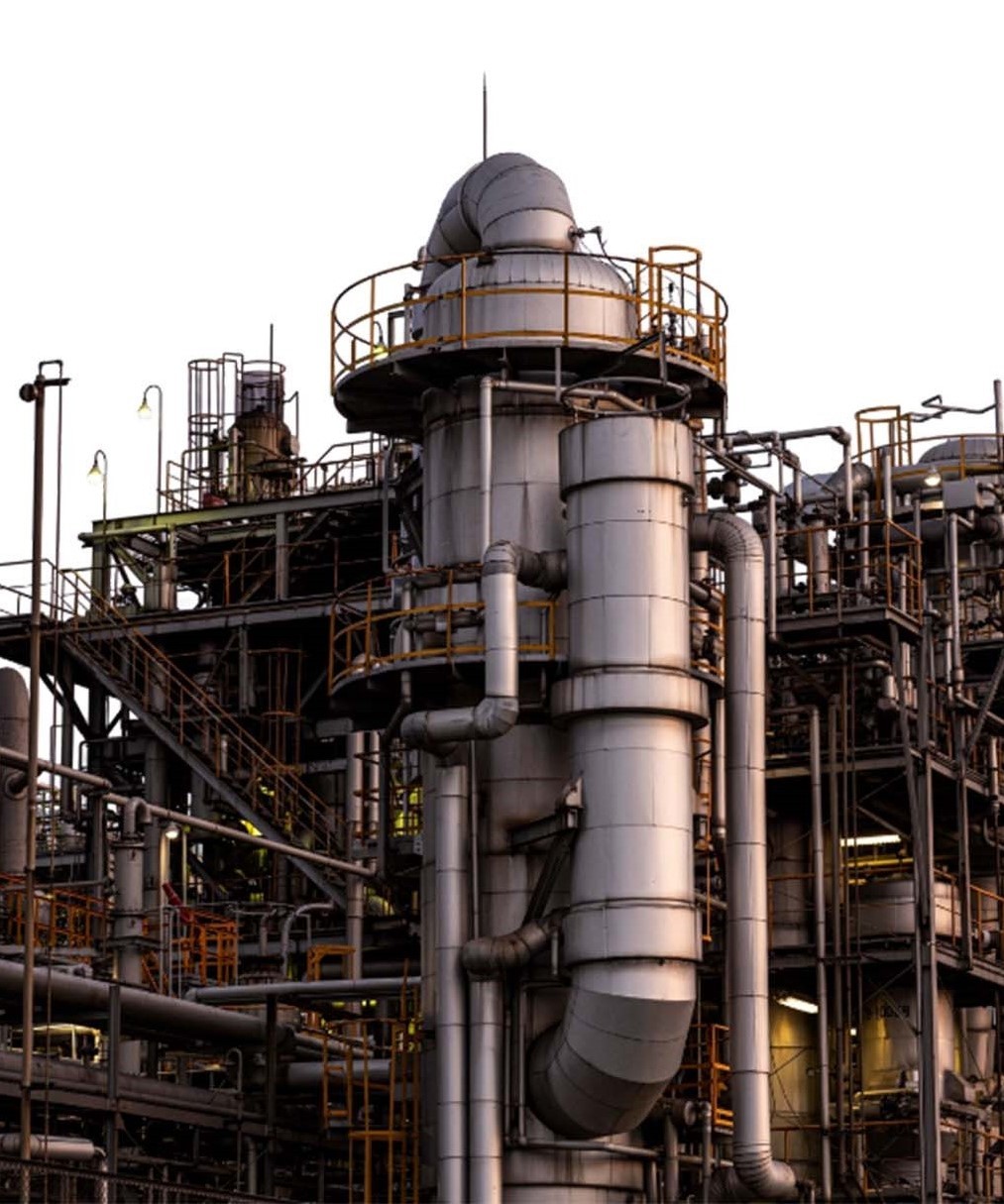
Refining
When it comes to downstream activities in the oil and gas industry, refining is at the top of the list. Here electric motors can be found in every step of the refining process, making for a huge number of them, thus complicating regular condition monitoring processes. By using Artesis technology you will reduce the time and labor to conduct a proper condition monitoring process. Monitor your Fluid Catalytic Unit (FCC) also known as the “cat cracker”, consider the heart of the refinery, without the need of installing any expensive sensors that may (or may not) withstand the higher temperatures generated in this process. Some other important steps where Artesis technology can be very useful are Sulfur Recovery, Distillation, Water Treatment, Alkylation, among others where pumps, compressors, and fans are essential. In addition, with the Artesis technology, you will be able to, without much effort, monitor all air compressors, fans, and other rotating equipment driven by electric motors which are numerous in any refining facility.
Drilling
All types of drilling rigs (fixed, compliant towers, floating, drillships, tension-let, subsea systems, sea-star, spar) are autonomous in energy and water needs, housing electrical generation, water declinators and all of the machinery to process oil and gas in a way that it can be either delivered directly onshore by pipeline or to a floating storage unit or tanker loading facility. However, there are many risks due to the extraction of volatile substances under extreme pressure in a hostile environment. Artesis technology can detect machinery problems far before they become a tragedy. Drilling machines, draw works, mud pumps, sheaves, and thrusters can be monitored continuously without installing sensors in hazardous areas.
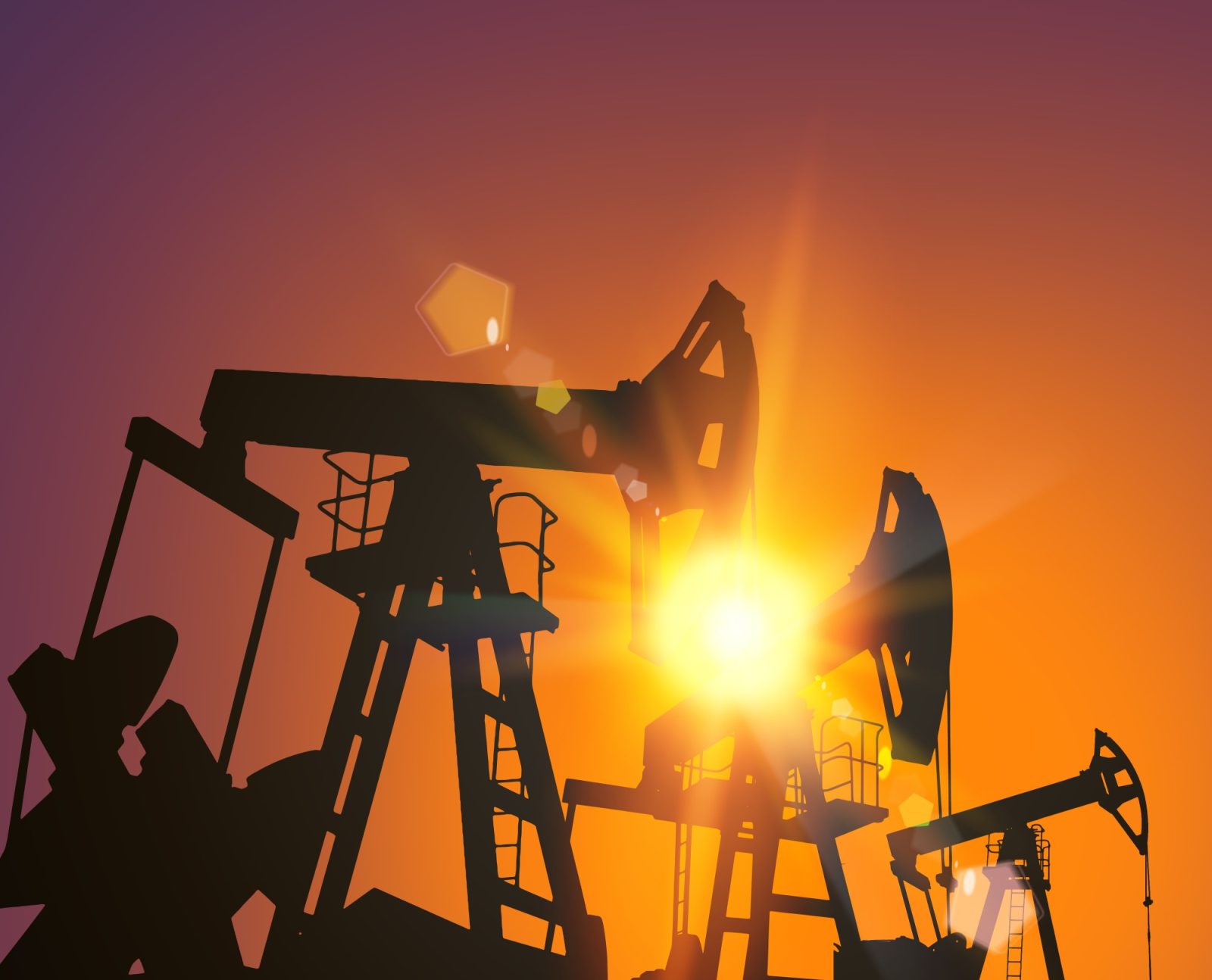
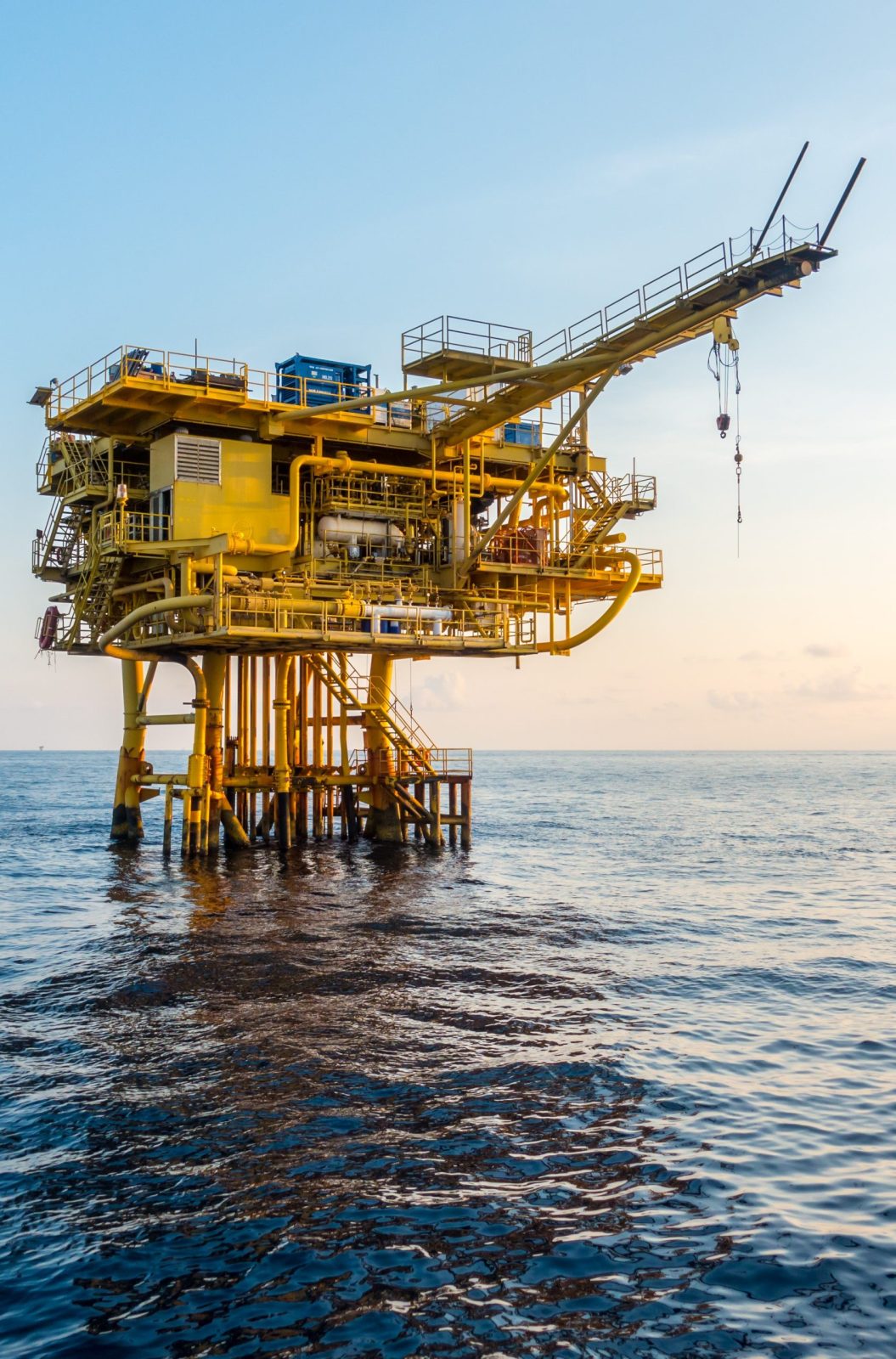
LNG
The liquefaction process demands machinery that operates under extreme conditions. Artesis technology offers continuous monitoring for reciprocating compressors utilized in the liquefaction process, along with gas turbines and cryogenic pumps. Artesis, being non-invasive and relying solely on current and voltage, is the perfect match for this application, ensuring efficient and reliable monitoring without disruption.
Offshore
Artesis offers effective solutions to enhance production efficiency and safety across various semi-submersible platforms and floating production units. We understand the unique difficulties faced by offshore platforms, dealing with harsh environmental conditions and intricate machinery, including reciprocating compressors, gas turbines, cryogenic pumps, and subsea pumps. We specialize in real-time and predictive monitoring, providing valuable insights into the health of each machinery asset in your offshore fleet. Our user-friendly cloud option ensures data privacy and security, seamlessly integrating with your local network. Using Artesis will help you to overcome offshore challenges and optimize the performance of your essential assets.
Application Areas in the Oil & Gas Sector


Compressors: Ensuring reliable operation of gas compressors used in natural gas extraction and processing.
Drilling Equipment: Monitoring motors and drives used in drilling rigs to prevent failures and downtime.
Offshore Platforms: Condition monitoring of rotating equipment under harsh offshore conditions.


Compressors: Ensuring fault-free operation of compressors at gas transportation hubs.
Storage Facilities: Monitoring rotating machinery in oil and gas storage tanks and terminals to prevent disruptions.


Compressors: Condition monitoring of hydrogen compressors and air compressors in refinery processes.
Cooling Towers: Monitoring motors driving cooling fans and water pumps in refining operations.
Distribution Systems: Ensuring reliability of pumps and motors at fueling stations and distribution terminals.


HVAC Systems: Ensuring efficient operation of fans, blowers, and pumps in ventilation systems at facilities.
Water Treatment Plants: Monitoring motors and pumps in water injection and produced water treatment systems.


Artesis and Jacobs Engineering Successfully Resolve Capacitive Coupling Issue
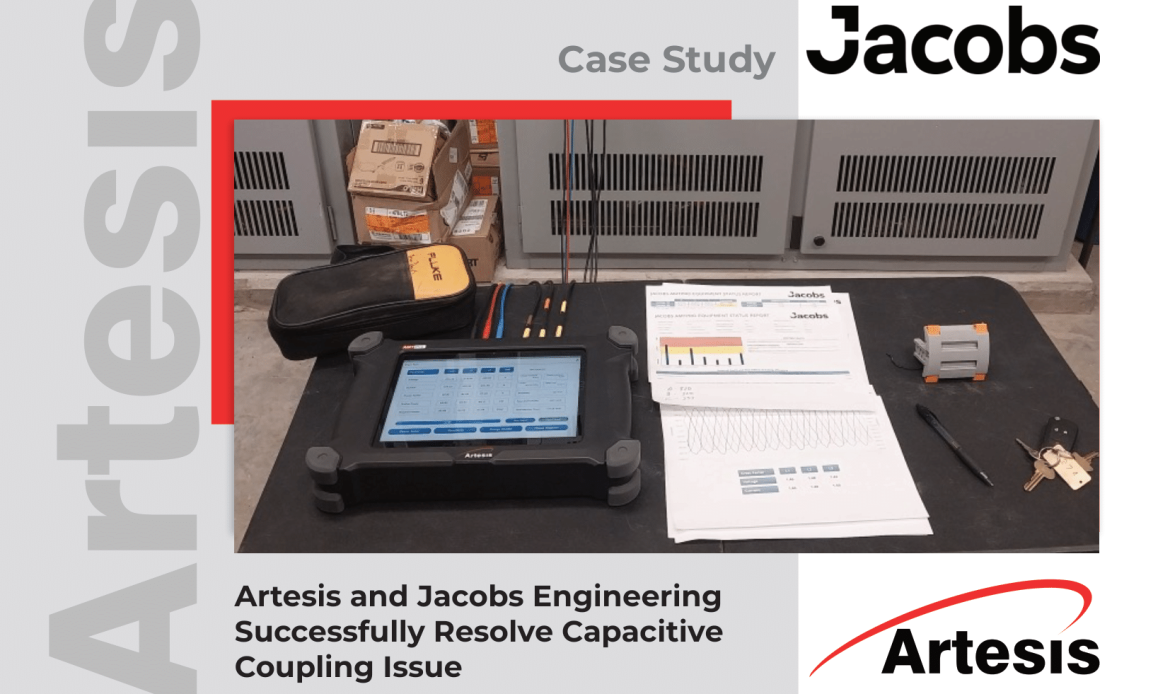