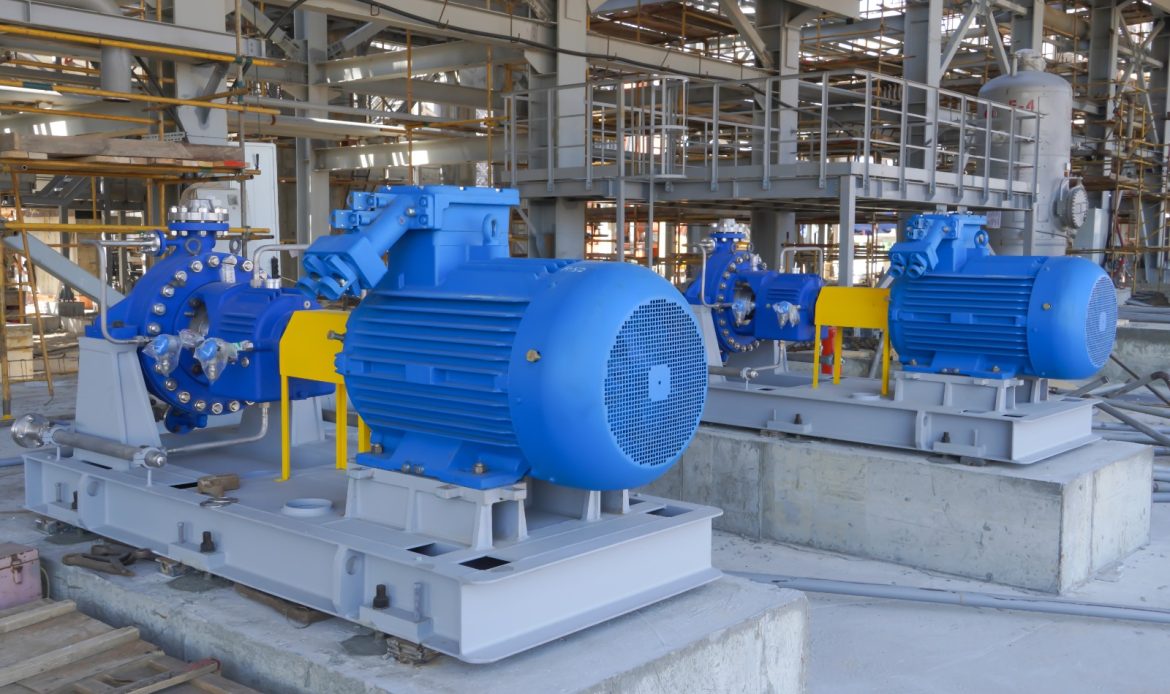
Choosing the right maintenance strategy is essential for improved reliability and availability of rotating equipment for more sustainable and profitable production. Especially with the impact of digitalization and IoT enhancement, more active and condition-based predictive maintenance methods have become increasingly prevalent daily. In this article, we will share 5 tips that might help you determine a condition-based maintenance strategy for your organization.
Contents
Start by Monitoring the Correct Assets
Condition-based monitoring is the most effective approach in machinery maintenance. A reactive maintenance approach only moves in after things have already gone wrong. At this point, smart facilities have early fault detection systems that warn at the early stage of faults before it is too late to intervene in faulty equipment. With this preventive approach, online condition-based monitoring always ensures the supervision of the machinery by the maintenance team. So, the maintainers only act when necessary and before an issue causes downtime in the equipment.
FOR MORE INFORMATION : MODEL BASED CONDITION MONITORING
Here is the tip! You may start monitoring by choosing frequently faulted assets that can easily give outcomes quickly. The more of these assets you can define and monitor, the higher the impact of the positive reactions will be. This strategy will help boost the confidence in condition-based maintenance within your organization.
Choose the Right Technology
It may take some time for you to choose the right technology, as many different condition monitoring technologies are available. Therefore, before selecting a condition monitoring technology, it will be helpful for you to ask the following questions.
1-Does it require sensor usage?
2-Are the equipment appropriate for this technology?
3-Is the technology suitable for the relevant environmental conditions affecting the equipment?
4-Do the implementation and learning processes require any expertise?
5-Does it have a digital infrastructure?
6-Is it a cost-effective option for our plant?
Trust the Power of Data
Condition-based monitoring is like installing a health tracker on industrial equipment. You can continuously compare the data from the equipment with the default condition and identify any potential faults months in advance. Especially for critical equipment, the more accurately and adequately the data is measured, the more precise you will get results from condition monitoring in terms of future malfunctions. At this point, you may be confused about collecting accurate data from dangerous and hard-to-access equipment.
Count on Digital Solutions
Digitalization and industry 4.0 provide innovative solutions for businesses in every field. The same goes for condition-based monitoring solutions. With a digital condition monitoring solution, you can track your assets 24/7 wherever you are, store the data, and have an effective digital solution without installing any software. You can even integrate your condition monitoring system with your existing SCADA solution and have a smart factory solution.
Digitalization would be the key when monitoring equipment in challenging locations.
Focus on the KPIs
An online condition monitoring system is a solution that has a positive impact on many departments in the factory. Ask the departments to establish KPIs to focus on to popularize and fully embrace the condition-based monitoring system at your organization.
For example;
1-Reduction in maintenance expenses
2-Reduction in unscheduled downtime
3-Inventory costs
4-Troubleshooting time
5-Product quality deliverables
6-Positive outcomes in work safety
As Artesis, we offer a digital and innovative solution for monitoring your critical equipment with our sensorless condition monitoring system. Contact us right now to meet the Artesis technology.