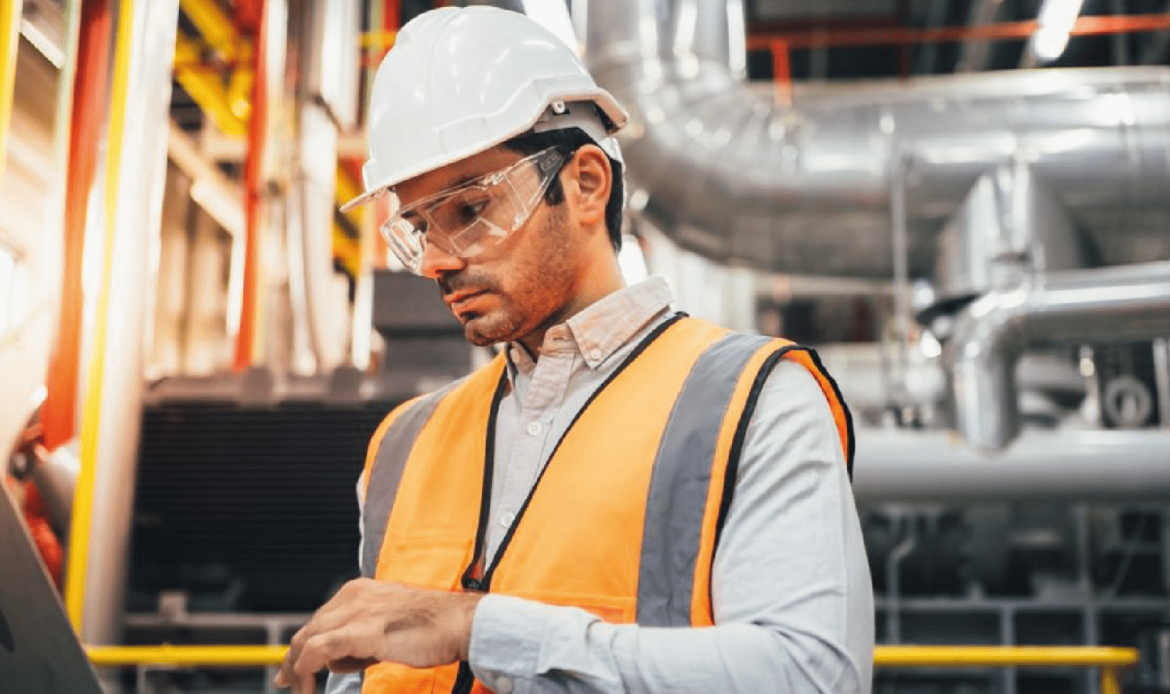
Ориентирование в сложном мире промышленного обслуживания может ощущаться как попытка решить гигантскую головоломку. Каждый элемент должен идеально подходить для бесперебойной работы оборудования. Но как измерить успех и убедиться, что ваша команда движется в правильном направлении? Все сводится к нахождению тех ключевых показателей эффективности (КПЭ), которые действительно имеют значение. Представьте КПЭ как компас вашей команды, направляющий вас через трудности работы по техническому обслуживанию и указывающий путь к эффективности и надежности. Итак, прежде чем мы углубимся в детали, давайте подготовим почву для понимания того, почему выбор правильных КПЭ может иметь решающее значение для вашей команды. Мы выясним, как команда промышленного обслуживания может оптимизировать операции и достичь своих целей более эффективно.
Contents
- 1 Сокращение внеплановых простоев: ключ к операционному совершенству
- 2 Максимизация надежности с помощью среднего времени между отказами (MTBF)
- 3 Ориентирование в водах реактивных часов работы по техническому обслуживанию
- 4 Повышение эффективности производства с помощью процента планового технического обслуживания (PMP)
- 5 Максимизация производства через общую эффективность оборудования (OEE)
- 6 «Правильное» решение для помощи промышленным командам технического обслуживания?
Сокращение внеплановых простоев: ключ к операционному совершенству
Неожиданные остановки представляют собой значительную проблему для предприятий, которые сильно зависят от непрерывности операций. Поразительная реальность заключается в том, что отрасли сталкиваются со средней стоимостью простоя в четверть миллиона долларов в час, что подчеркивает серьезность незапланированных остановок. Тревожно то, что 70% предприятий не полностью осведомлены о том, какие из их активов требуют технического обслуживания, что приводит к внезапным отказам и дорогостоящим периодам бездействия. Внедрение стратегического плана технического обслуживания могло бы сократить время простоя на существенную величину, превышающую 30% в некоторых случаях.
КПЭ, сосредоточенные на отслеживании внеплановых простоев, бесценны для руководителей по техническому обслуживанию, предоставляя призму, через которую можно оценить эффективность стратегий технического обслуживания. Понимание широкого воздействия простоев имеет решающее значение, поскольку оно напрямую коррелирует с операционными издержками и потерями производительности, что делает императивным для предприятий стремление к минимальным нарушениям в их деятельности.
Максимизация надежности с помощью среднего времени между отказами (MTBF)
MTBF, или среднее время между отказами, является критически важным показателем для любого специалиста в области технического обслуживания. Он показывает, как долго обычно работает единица оборудования до того, как выйдет из строя. Представьте это как оценку, которая говорит вам, насколько надежны ваши машины. Проще говоря, MTBF помогает понять, как часто вам придется ремонтировать вещи, которые можно починить, такие как двигатели, насосы или конвейерные ленты. Это отличается от предметов, которые нельзя отремонтировать после поломки, где вы бы рассматривали другой показатель, называемый средним временем до отказа (MTTF).
Стратегия технического обслуживания на основе состояния в 5 шагов
Для примера рассмотрим производственный сценарий, где линия розлива испытывает эксплуатационные сбои с интервалами. Если в течение года линия выходит из строя только три раза, с периодами эксплуатации 120, 150 и 180 дней соответственно между отказами, расчет MTBF предоставил бы ценные сведения о надежности линии, направляя стратегии технического обслуживания на повышение времени безотказной работы и эффективности.
Ориентирование в водах реактивных часов работы по техническому обслуживанию
Этот КПЭ отслеживает время, затраченное на решение незапланированных ремонтов или чрезвычайных ситуаций, предоставляя моментальный снимок того, сколько усилий направлено на устранение проблем по мере их возникновения. Этот показатель жизненно важен для понимания баланса между профилактическими и срочными задачами технического обслуживания в организации. Высокие часы реактивного обслуживания могут указывать на необходимость более надежных профилактических мер или сигнализировать о частых отказах оборудования, влияющих на общую производительность и эксплуатационные расходы. Отслеживая эти часы, команды могут выявлять тенденции, более эффективно распределять ресурсы и стремиться к более прогностическому подходу к техническому обслуживанию.
Повышение эффективности производства с помощью процента планового технического обслуживания (PMP)
Этот ключевой показатель эффективности измеряет долю работ по техническому обслуживанию, которые планируются и назначаются заранее, в сравнении с реактивными или аварийными работами. Этот КПЭ критически важен, поскольку он напрямую влияет на эффективность и надежность операций. Высокий PMP указывает на проактивную стратегию технического обслуживания, которая может привести к сокращению простоев, снижению затрат на ремонт и улучшению долговечности активов. Сосредоточившись на плановом обслуживании, команды могут обеспечить более гладкие операции, минимизировать сбои и точнее прогнозировать будущие потребности в техническом обслуживании, повышая общую производительность.
Максимизация производства через общую эффективность оборудования (OEE)
Данный комплексный показатель оценивает эффективность использования оборудования в производственном процессе. Он объединяет метрики доступности, производительности и качества, предоставляя единый показатель, отражающий процент действительно продуктивного производственного времени.
5 ключевых преимуществ мониторинга состояния ременных систем
Оптимальный показатель OEE свидетельствует о том, что предприятие производит товары с максимальной скоростью, без дефектов и с минимальными простоями. Отслеживание OEE помогает командам технического обслуживания выявлять области для улучшения производственного процесса, стремясь устранить потери, предотвратить отказы оборудования и обеспечить качество продукции, тем самым способствуя операционному совершенству и конкурентоспособности.
«Правильное» решение для помощи промышленным командам технического обслуживания?
Промышленные команды технического обслуживания могут получить значительные преимущества, внедрив технологию Artesis в свои операции. Эта технология упрощает процесс предиктивного обслуживания, обеспечивая беспрепятственный мониторинг и простое, легко понятное представление данных. Благодаря интуитивно понятной системе предупреждений по принципу «светофора» и автоматическому уведомлению о неисправностях, отправляемому непосредственно на человеко-машинные интерфейсы (HMI) и по электронной почте, команды имеют возможность предвидеть потенциальные проблемы. Технология Artesis способна выявлять потенциальные отказы за шесть месяцев до их возникновения, обращая внимание на такие проблемы, как необычные вибрации, перегрев или аномальные шумы. Более того, она способствует выполнению точных действий по техническому обслуживанию с уровнем точности, превышающим 90%. Такой проактивный подход не только повышает надежность оборудования, но и оптимизирует графики технического обслуживания, сокращая время простоя и повышая операционную эффективность. Пожалуйста, свяжитесь с нами, если у вас возникнут дополнительные вопросы или вы захотите заказать демонстрацию.