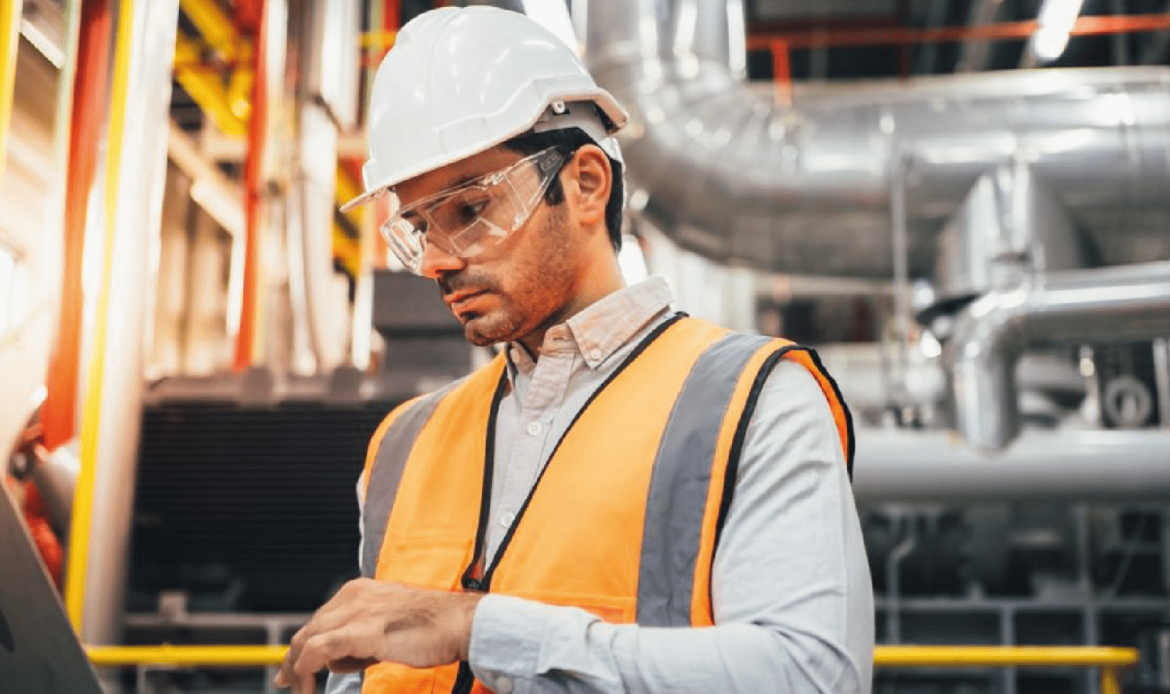
Naviguer dans le monde complexe de la maintenance industrielle peut s’apparenter à la résolution d’un puzzle gigantesque. Chaque pièce doit s’ajuster parfaitement pour que la machinerie fonctionne sans accroc. Mais comment mesurer le succès et s’assurer que votre équipe est sur la bonne voie ? Tout réside dans l’identification des indicateurs de performance clés (KPI) véritablement pertinents. Considérez les KPI comme la boussole de votre équipe, vous guidant à travers les défis du travail de maintenance et vous orientant vers l’efficacité et la fiabilité. Avant d’aborder les spécificités, posons le cadre pour comprendre pourquoi le choix des bons KPI peut faire toute la différence pour votre équipe. Nous découvrirons comment l’équipe de maintenance industrielle peut affiner ses opérations et atteindre ses objectifs de manière plus efficiente.
Contents
- 1 Réduction des Temps d’Arrêt Non Planifiés : Une Clé de l’Excellence Opérationnelle
- 2 Maximiser la Fiabilité avec le Temps Moyen Entre Pannes (MTBF)
- 3 Naviguer dans les Eaux des Heures de Travail de Maintenance Réactive
- 4 Améliorer l’Efficacité de la Fabrication avec le Pourcentage de Maintenance Planifiée (PMP)
- 5 Maximiser la Production grâce à l’Efficacité Globale des Équipements (OEE)
- 6 La solution « appropriée » pour aider les équipes de maintenance industrielle ?
Réduction des Temps d’Arrêt Non Planifiés : Une Clé de l’Excellence Opérationnelle
Les arrêts inopinés constituent un revers significatif pour les entreprises dépendant fortement d’opérations continues. La réalité saisissante est que les industries font face à un coût moyen de temps d’arrêt d’un quart de million de dollars par heure, un chiffre qui souligne la gravité des interruptions non planifiées. De manière alarmante, 70% des entreprises ne sont pas pleinement conscientes des actifs nécessitant une maintenance, conduisant à des défaillances soudaines et à des périodes d’inactivité coûteuses. La mise en œuvre d’un plan de maintenance stratégique pourrait réduire les temps d’arrêt d’une marge substantielle, dépassant 30% dans certains cas.
Les KPI axés sur le suivi des temps d’arrêt non planifiés sont inestimables pour les superviseurs de maintenance, offrant une perspective à travers laquelle l’efficacité des stratégies de maintenance peut être évaluée. Comprendre l’impact global des temps d’arrêt est crucial, car il est directement corrélé aux coûts opérationnels et aux pertes de productivité, rendant impératif pour les entreprises de s’efforcer de minimiser les perturbations dans leurs opérations.
Maximiser la Fiabilité avec le Temps Moyen Entre Pannes (MTBF)
Le MTBF, ou Temps Moyen Entre Pannes, est une mesure cruciale pour quiconque dans le domaine de la maintenance. Il indique combien de temps un équipement fonctionne typiquement avant de tomber en panne. Considérez-le comme un score qui vous renseigne sur la fiabilité de vos machines. En termes plus simples, le MTBF vous aide à comprendre à quelle fréquence vous devrez réparer des éléments réparables, tels que des moteurs, des pompes ou des convoyeurs. Ceci diffère des articles que vous ne pouvez pas réparer une fois brisés, pour lesquels vous examineriez une mesure différente appelée Temps Moyen Jusqu’à Défaillance (MTTF).
À titre d’exemple, considérons un scénario de fabrication où une chaîne d’embouteillage connaît des défaillances opérationnelles à intervalles. Si sur une année, la ligne ne tombe en panne que trois fois, avec des périodes opérationnelles de 120, 150 et 180 jours respectivement entre les pannes, le calcul du MTBF offrirait des insights précieux sur la fiabilité de la ligne, guidant les stratégies de maintenance pour améliorer le temps de fonctionnement et l’efficacité.
Cet indicateur de performance clé suit le temps consacré à traiter les réparations non planifiées ou les urgences, offrant un aperçu de la quantité d’efforts dirigés vers la résolution des problèmes au fur et à mesure qu’ils surviennent. Cette métrique est vitale pour comprendre l’équilibre entre les tâches de maintenance préventive et urgente au sein d’une organisation. Un nombre élevé d’heures de maintenance réactive peut indiquer un besoin de mesures préventives plus robustes ou signaler des défaillances fréquentes d’équipement, affectant la productivité globale et les coûts opérationnels. En surveillant ces heures, les équipes peuvent identifier les tendances, allouer les ressources plus efficacement et s’efforcer d’adopter une approche de maintenance plus prédictive.
Améliorer l’Efficacité de la Fabrication avec le Pourcentage de Maintenance Planifiée (PMP)
Cet indicateur de performance clé mesure la proportion de travaux de maintenance planifiés et programmés à l’avance par rapport aux travaux réactifs ou d’urgence. Ce KPI est crucial car il impacte directement l’efficacité et la fiabilité des opérations. Un PMP élevé indique une stratégie de maintenance proactive, pouvant conduire à une réduction des temps d’arrêt, des coûts de réparation inférieurs et une longévité accrue des actifs. En se concentrant sur la maintenance planifiée, les équipes peuvent assurer des opérations plus fluides, minimiser les perturbations et prédire plus précisément les besoins futurs en maintenance, améliorant ainsi la performance globale.
Maximiser la Production grâce à l’Efficacité Globale des Équipements (OEE)
Cette métrique globale évalue l’efficacité avec laquelle une opération de fabrication utilise son équipement. Elle combine les indicateurs de disponibilité, de performance et de qualité pour fournir un chiffre unique qui reflète le pourcentage de temps de fabrication véritablement productif.
5 avantages clés de la surveillance de l’état des systèmes de courroies
Un score OEE optimal indique qu’une usine produit des biens à vitesse maximale, sans défauts, et avec le moins d’arrêts possible. Le suivi de l’OEE aide les équipes de maintenance à identifier les domaines d’amélioration dans le processus de production, visant à éliminer les gaspillages, prévenir les pannes d’équipement et assurer la qualité des produits, favorisant ainsi l’excellence opérationnelle et la compétitivité.
La solution « appropriée » pour aider les équipes de maintenance industrielle ?
Les équipes de maintenance industrielle peuvent tirer des avantages significatifs en incorporant la technologie Artesis dans leurs opérations. Cette technologie simplifie le processus de maintenance prédictive, permettant une surveillance sans faille et une présentation des données claire et facilement compréhensible. Grâce à son système d’avertissement intuitif à « feux de signalisation » et à la notification automatique des défauts envoyée directement aux interfaces homme-machine (IHM) et par courriel, les équipes sont équipées pour anticiper les problèmes potentiels. La technologie Artesis peut identifier les défaillances potentielles jusqu’à six mois avant leur survenue, mettant en évidence des problèmes tels que des vibrations inhabituelles, une surchauffe ou des anomalies sonores. De plus, elle facilite l’exécution d’actions de maintenance précises avec un taux de précision dépassant 90%. Cette approche proactive améliore non seulement la fiabilité des équipements, mais optimise également les calendriers de maintenance, réduisant les temps d’arrêt et augmentant l’efficacité opérationnelle. Veuillez nous contacter si vous avez d’autres questions ou si vous souhaitez réserver une démonstration.